Once a luxury only few could afford and now an almost commonplace dye, indigo’s mark on history is irrefutable.
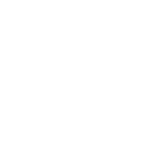
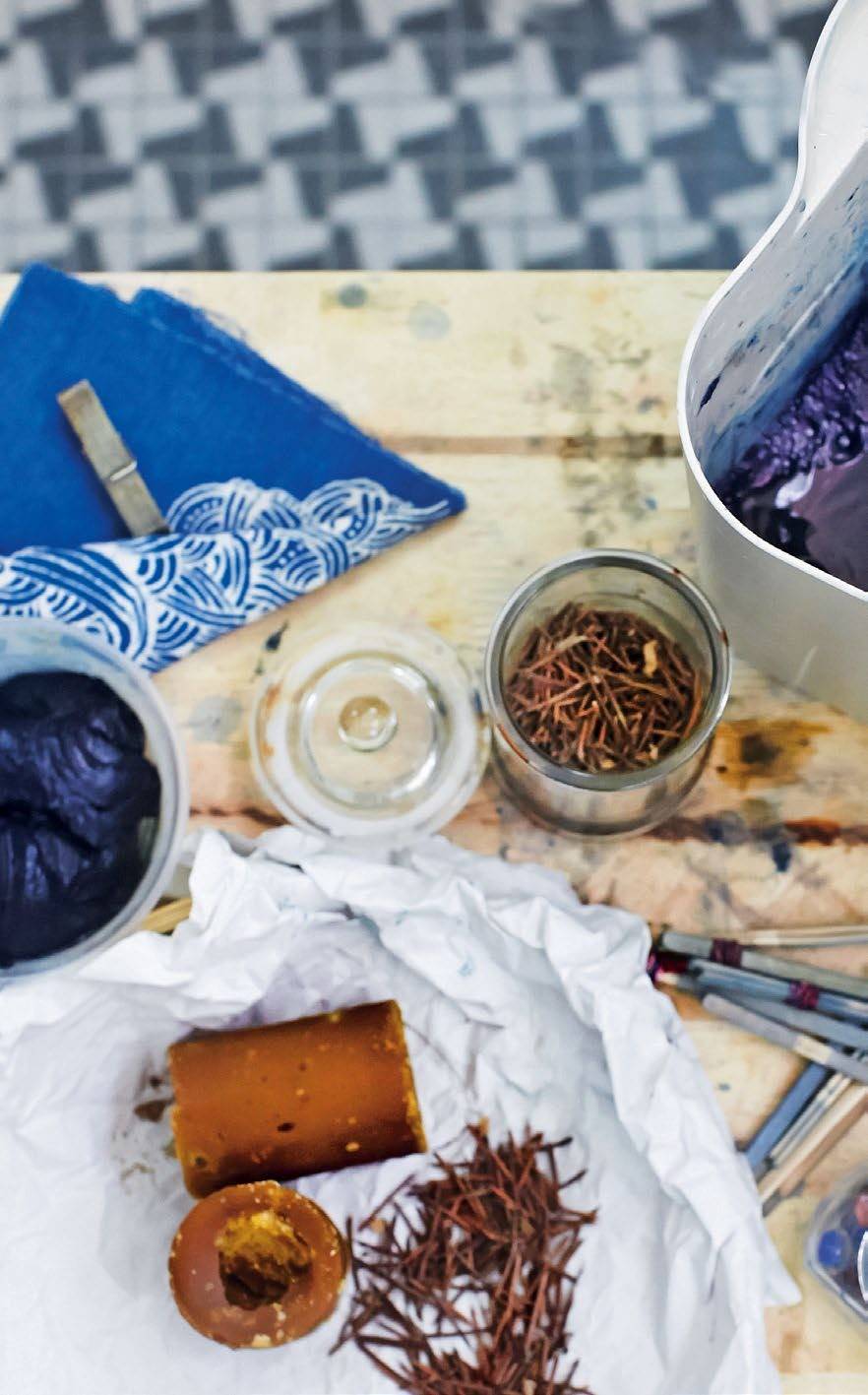
From lining the borders of Egyptian linen mummy wrappings around 2,400BC to being worn beneath Japanese samurai armour to keep bacteria away from their wounds, indigo – nicknamed “blue gold” at the height of its popularity – has stamped history with a presence that goes way back to Japanese, Indian, Egyptian and ancient Mayan cultures. And while the world may have seen a drop in the demand for the natural dye before, the resurgence of ecofriendly fabrics and ethical clothing in the fashion industry has sparked an indigo revival.
Indigo is extracted from the Indigofera tinctoria and is characterised by its intense blue hue and natural antiseptic qualities. Naturally occurring in most tropical countries – ranging from Australia to South-east Asia, and most African countries – Indigofera tinctoria is just one of the 50 species of indigo-bearing plants that researchers have identified. In fact, even with a plethora of indigobearing plants around the world, there is no single point of origin from which the dye was first recognised and utilised. However, many believe that India was the main, if not biggest, producer of indigo dye collected from indigo-bearing genus and not woad, a flowering plant that produces a similar shade to indigo. As the British opened India up to European trade, indigo cakes or pressed indigo, were delivered to many European countries.
“Two millennia ago, when dried indigo pigment was exported to Europe from India, it was reserved for paint and cosmetics. But a wonderful feature of indigo is that it will colour all kinds of fibres and this made it a dye for the working person wearing practical fabrics, as well as the dye for luxury silks,” said Jenny Balfour-Paul, in an interview with The Peak. She has held a long-time passion for the art of indigo dyeing with a career spanning over 40 years, and has three books to her name, Indigo in the Arab World, Indigo: Egyptian Mummies to Blue Jeans, and Deeper Than Indigo: Tracing Thomas Machell, Forgotten Explorer.
Indigo dyeing is a traditional process that requires patience, a skilled hand and craftsmanship refi ned by years of training. In Japan, it is a revered tradition and part of the nation’s cultural DNA with places like Higeta Aizome Kobo or Higeta Indigo Dyeing Studio, one of the longest running indigo production houses run by the original family. Founded in the Edo period (1603-1868), the studio uses only the original traditional dyeing method, and if one is willing to stay and watch the entire process, one might even catch a glimpse of the famous Shibori tie-dye technique, local to Japan.
“One of the main fascinations about indigo is the way in which diff erent cultures have developed their own ways that are best suited to local conditions. I love to watch diff erent dyers around the world use their own methods, and the ideal is a true fermentation dye vat,” said Balfour-Paul. Her love for the dye has led to her planting various indigobearing plants and using a diverse array of methods to achieve the dye, simply as a way to understand the various facets of the indigo.
This luxury commodity was dethroned in 1867, when German chemist Adolf von Baeyer created synthetic indigo and had it commercially manufactured in 1897. Today, an overwhelming demand for the saturated blue dye has led to its mass production, with just over 50,000 tonnes of synthetic indigo fabric being churned out in 2018 alone.
On top of this, sustainable fashion is rapidly catching on among many big brands opting to join the cause and do away with “fast fashion”, and a strong side effect of this following is the renaissance of a handmade natural process to treat clothes and cloths. Indigo dyeing falls under this category. One of the few Malaysian artisans to have stained her hands blue while making indigo products using the traditional process is Ummi Kalthum Junid, owner of Dunia Motif, a company she runs from her home studio. She talks about how she got into the indigo dyeing business. and what she hopes people will appreciate about this painstaking passion.
When did your interest in making indigo dye begin, and have you always been interested in creating natural dyes?
I have always loved looking at designs and exploring patterns from around the world. One of the interesting patterns that I felt a strong connection to was the Gurunsi House pattern from Burkina Faso. In 2014, I got the opportunity to work in Sierra Leone, West Africa. There, I explored African batik and was drawn to the colour making involving synthetic material such as remazol. As I explored further, I realised some colours could be made from flowers and vegetables, and this triggered my interest in the field.
What is in Dunia Motif’s future?
As Dunia Motif grows, I would like to turn it into a textile art centre in Malaysia. It is a huge dream of mine because I have a much bigger plan in place for the operation. I would love to have a team of textile artisans – from batik designers to weavers, dyers, and tailors – come together and share their passion by teaching the younger generation about textiles. In Europe the concept of “slow fashion” was introduced about 10 to 15 years ago. In Malaysia, we also have the potential to practise the same concept.
How did you learn about the art of indigo dyeing?
Most of my experience has been from Indonesia. I find it easier to communicate there and it helps that we use nearly the same resources. I travelled all the way to Jlamprang and Semarang to learn indigo processing. Besides Indonesia, India also showcases interesting natural dye methods that I am keen on picking up. Youtube and Google have also been big sources of information that have helped me to combine both Western and Eastern techniques into my own process.
Is there a market out there for indigo products?
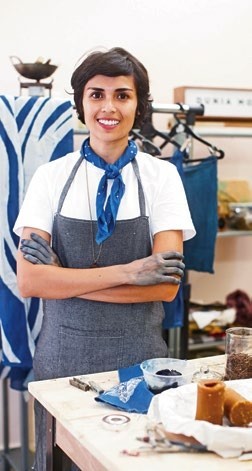
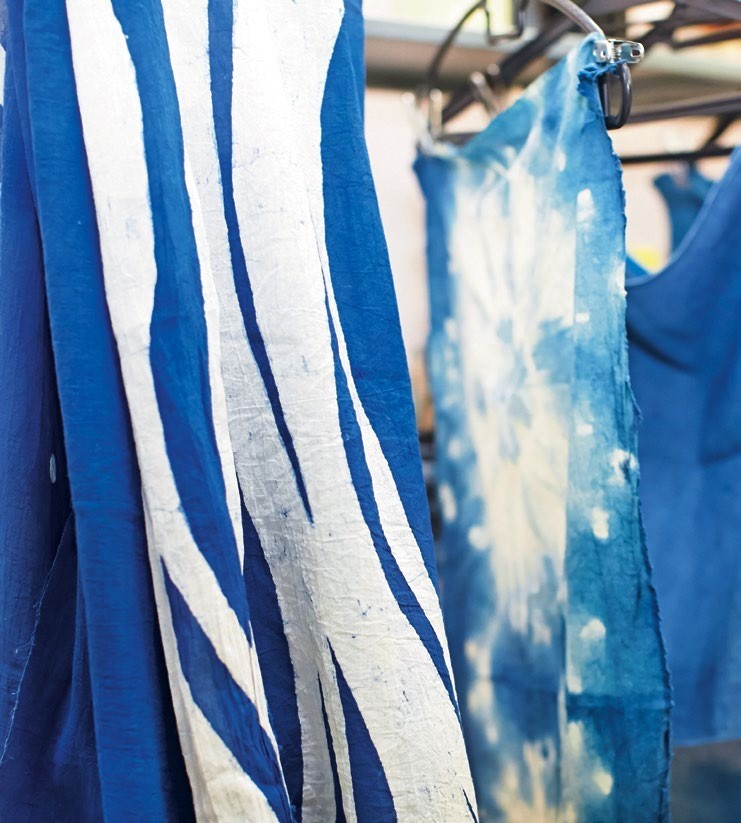
DO OR DYE: A GUIDE TO THE TRADITIONAL INDIGO DYEING PROCESS
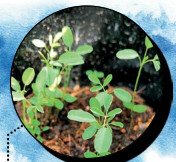
01 Plant Indigofera Tinctoria seed and keep watch for three to four months.

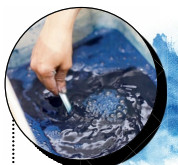
04 Drain the bundles of leaves and discard them, leaving the water behind. Gently mix in 2 per cent of builders lime into the coloured water.
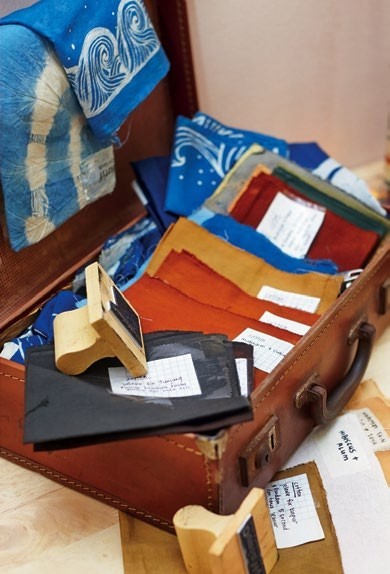
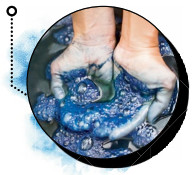
06 Once beaten, the water should change from a murky green to a peacock blue, before turning a frothy navy blue. The minute it hits navy and dark blue bubbles begin to form, the mixture is ready.
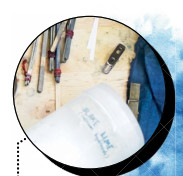
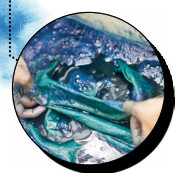
09 Continuously stir the mixture throughout the fermenting process.
10 Finally, dye cloth in the indigo vat. Dyed cloth may appear green at first but it will quickly turn blue from oxidisation. For a darker or lighter shade of indigo, dip the cloth in the vat multiple times.