A major new IWC production facility is the latest milestone in the brand’s traditional watchmaking-meets-high-tech story.
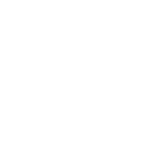
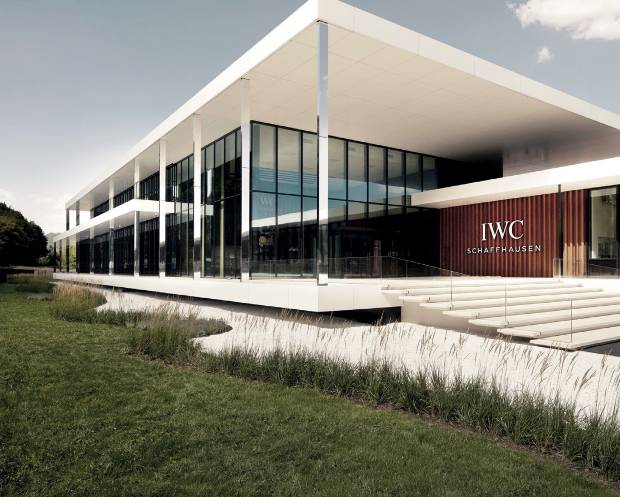
A major new IWC production facility is the latest milestone in the brand’s traditional watchmaking-meets-high-tech story.
There is no doubt that IWC’s new integrated facility is its pride and joy, and one that it is proud to show to the world. In our second outing to the heart of German-speaking Switzerland for the opening of the IWC Manufakturzentrum, there are absolutely no limits on photography or video-recording, and we practically breathe down the necks of some of the watchmakers. This is a far cry from four years ago, when we visited IWC’s headquarters and its other key facility at nearby Neuhausen, and strict restrictions were placed on photography, as well as where we could venture.
We would want to show it off , too: Located in Merishausen, a Schaffhausen municipality just a ten minute drive away from the brand’s headquarters on Baumgartenstrasse, the 13,500 sq m facility makes a definite first impression. Amid a thoroughly verdant setting, it is a long, low-lying building with a facade dominated by floor-to-ceiling glass windows and rigorously rectangular white concrete structures. Partly designed by the brand’s CEO, Christoph Grainger-Herr – an architect and interior designer by training – the facility is meant to see IWC at least 50 years into the future.
Housing key processes – including case and movement-part production, as well as movement assembly – under its massive roof, the Manufakturzentrum brings together 239 skilled workers and high-precision machines in a logical, continuous production flow.
“We don’t just celebrate candlelight romance,” says Grainger-Herr with a wry smile, during a roundtable interview. “In watchmaking, there are times when the human touch is the only thing that makes a difference. But it’s never a contradiction to have machine technology come together with the human hand. I don’t think we need to be afraid to use the best technology to make a better product.”
This two-pronged philosophy has guided IWC since 1868, when its American founder, Florentine Ariosto Jones, started his company in Schaffhausen in eastern Switzerland. In contrast to the cottage industry that defined watchmaking in western Switzerland, F.A. Jones combined Swiss watchmaking know-how with new American industrial production methods, driven by hydropower supplied by the nearby River Rhine. Today, the opening of the Manufakturzentrum brings that vision full circle.
Says Grainger-Herr: “I think the Manufakturzentrum is one of the most important selling points that we have. You fall in love with the brand, the design and the story, but here you can see that love, that craftsmanship, that dedication, the passion that goes into each and every IWC watch. It’s a beautiful reconfirmation of what this brand stands for.”
01 GO BIG
The new integrated IWC Manufakturzentrum covers a stunning 13,500 sq m in total area, but its expansiveness is not an end in itself. It was designed with growth and versatility in mind. With a maximum capacity of 400, there is room for almost double its current workforce of 239.
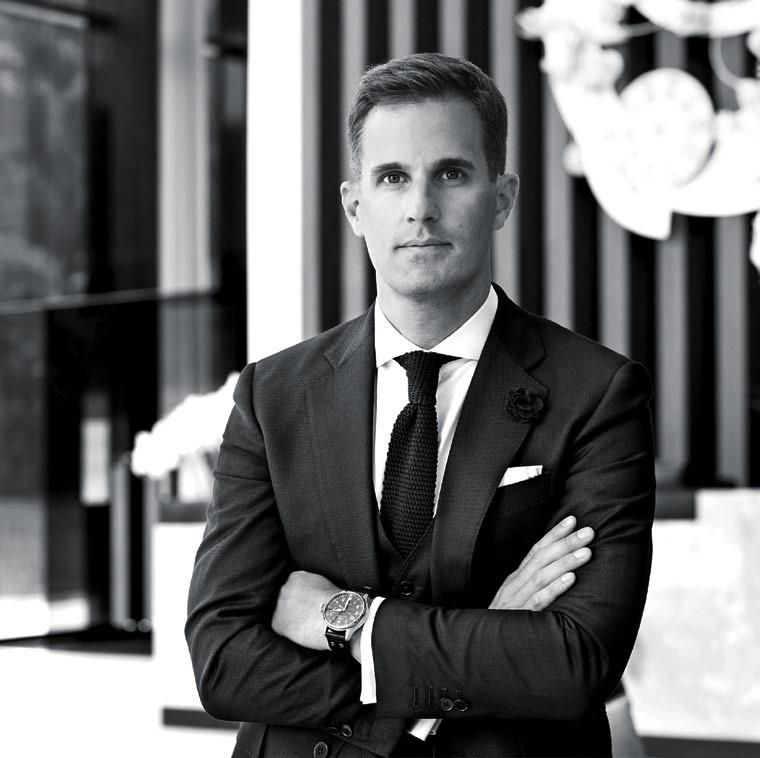
02 LEADING THE WAY
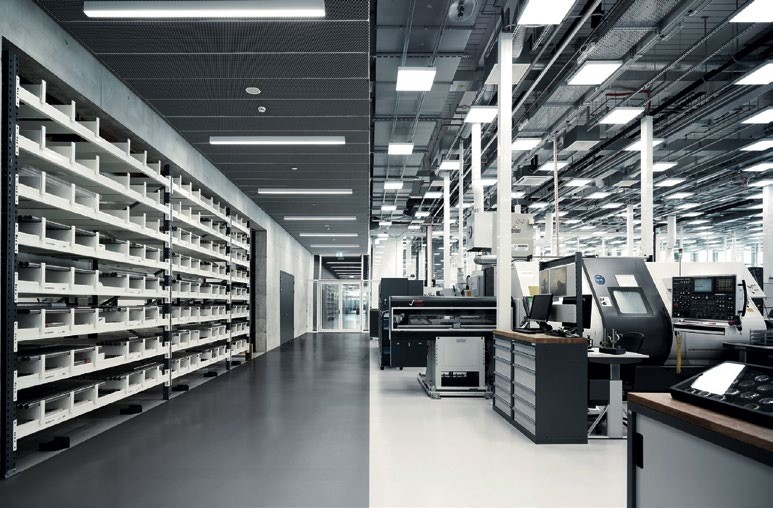
03 MATERIAL WORLD
BUILDING BLOCKS
The numbers behind the Manufakturzentrum.
COST
42m
Swiss francs
LENGTH
139m
WIDTH
62m
TOTAL FLOOR AREA
13.5k
sq m
TOTAL VOLUME
69.2k
cubic metres
GLASS FACADE
2.2k
sq m
STEEL STRUCTURAL FRAME OF BUILDING
840
tonnes
CONSTRUCTION PERIOD
21
months
CONSTRUCTION COMPANIES
80
SOLAR PANELS
2.2k
sq m providing up to 15% of energy for production
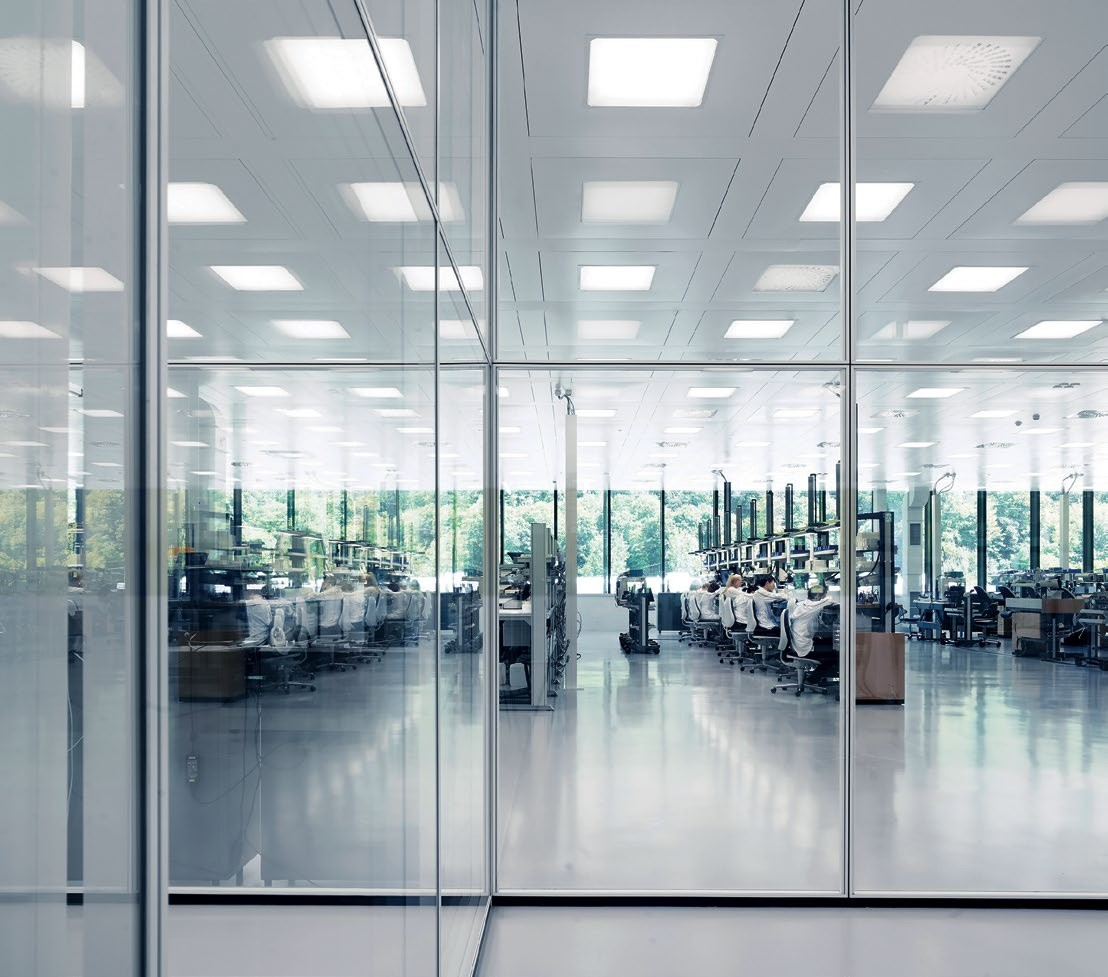
04 MOVEMENT ASSEMBLY
Movement assembly is carried out in a class-seven clean room (more on that later). While small-series movements such as that of the Tribute to Pallweber watch and complex modules like the perpetual calendar are still assembled the traditional, A-to-Z way over at headquarters, the line system applies to the assembly of all the movements at the Manufakturzentrum. These comprise the automatic movements of Calibre families 52 and 82, the Calibre family 59 hand-wound movements, and the Calibre 69 chronograph movements; as well as the new Portugieser Chronograph movement.
Explains IWC COO Andreas Voll: “Before one watchmaker was doing one movement from A to Z. Now, we have broken down the whole assembly process into multiple sub-processes, which allows us to assign dedicated watchmaking specialists to each production step.”
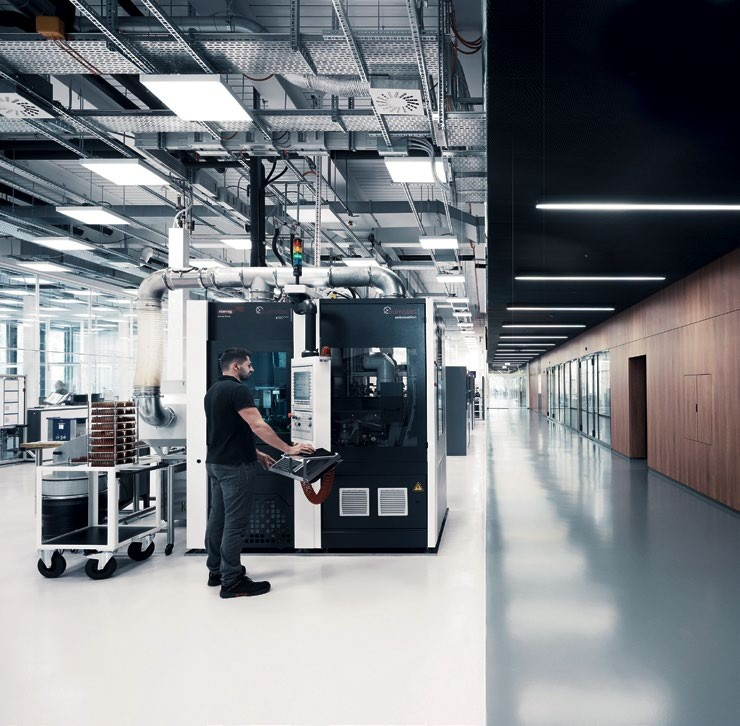
05 MOVEMENT-PART PRODUCTION
The building houses key processes such as case and movement part production, as well as movement assembly. Some 1,500 parts are produced at the movement component production workshop. These include components for base movements, as well as those for complications such as perpetual calendars, annual calendars and tourbillons. Because of the very low tolerances required for these parts – think accuracy to the thousandths of a millimetre – most of the processes here are automated.
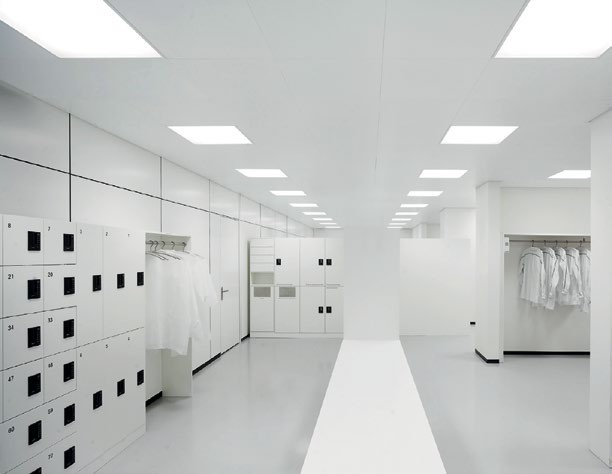
06 CLEAN WARDROBE
Watchmakers have to change into special, anti-static coats before entering the class seven clean room where movement assembly takes place.
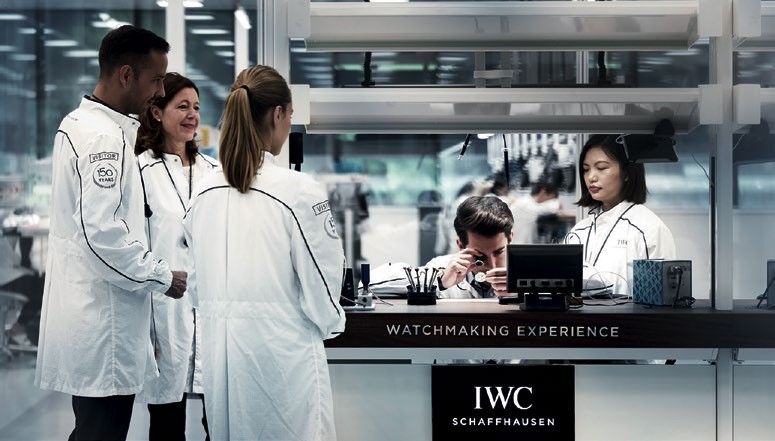
07 VISITOR INTERACTION
Two watchmaker workstations let visitors get hands on with tools of the trade.