Van Cleef & Arpels has unveiled one of its most ambitious projects yet: The Automate Fée Ondine. CEO Nicolas Bos walks us through the table clock’s intricacies.
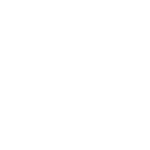
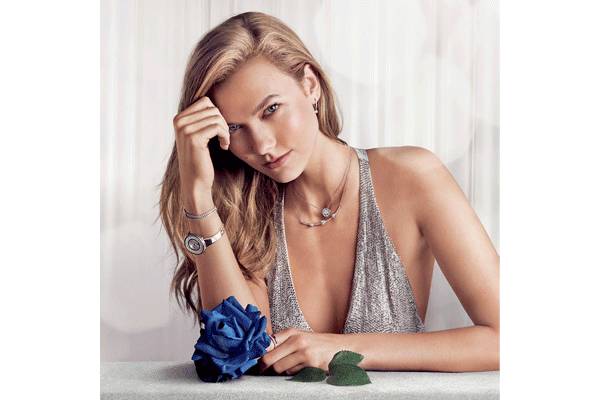
Van Cleef & Arpels has unveiled one of its most ambitious projects yet: The Automate Fée Ondine. CEO Nicolas Bos walks us through the table clock’s intricacies.
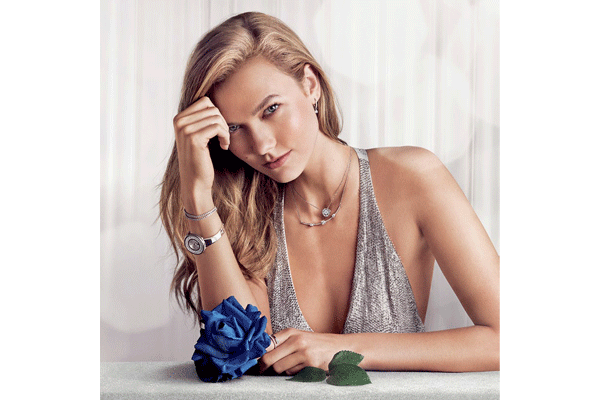
The Automate Fée Ondine is the first of its kind that Van Cleef & Arpels (VCA) has ever produced. Tell us more about it.
It’s something a bit unusual in the [VCA] collection, mostly because it doesn’t fall in the jewellery or the watch category. It’s more of an experimental, creative project that we started quite a long time ago and it has to do with the inspiration behind our Poetic Complications and narrative watches. The approach is quite rooted in the tradition of automatons, which is how to use a mechanical movement to create a kind of magical animation and give life to a story. We started talking about this about eight years ago to see if we could develop it. So we started to investigate on who was still making automatons, what kind of techniques were being used, and how we could do something that was an expression of the house—with the same stories we have for our watches—but with a more complex animation and longer scenario.
This extensive project called for a whole cast of collaborators. What was the process like?
We met with François Junod, one of the very few automakers today, and explored how we could do a piece that was an expression of his tradition and his art, but one that would also identify all aesthetic crafts and representations. So that took a lot of time to just define the project and its feasibility; then, the last three years were dedicated to its production. It’s a very long process to create a piece like that especially because of the complexity of the mechanism itself: There’s only a very small team of people who can do it. We have 20 different workshops and the coordination to make sure everything works smoothly takes a lot of back and forths.
So you worked with 20 different workshops for this?
Of course, we didn’t start with 20 workshops [laughs]. We started with very few, and then we found we needed to add more along the way. For instance, we started, really, with our jewellery and stone-setting workshops. Then, because of constraints—of weight and scale—we discovered there are quite a few things that we didn’t necessarily have the skills to do. We have a very good internal enamelling workshop that does all the dials of our watches. But when we started to work on the size of the leaf, it [required] a different technique using different ovens. So we went to different workshops that are more specialised in biggersized elements. Same for the lapidary work; we had to ask several different workshops for different types of stone-setting.