In the second of a two-part article, our mechanical engineer continues to explain the technology of active suspension.
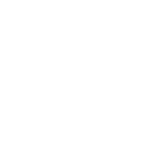
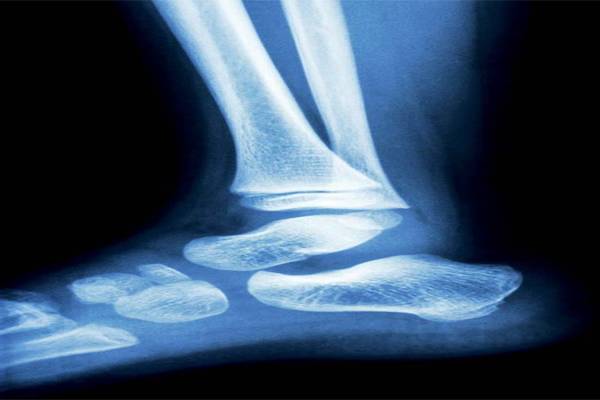
In the second of a two-part article, our mechanical engineer continues to explain the technology of active suspension.
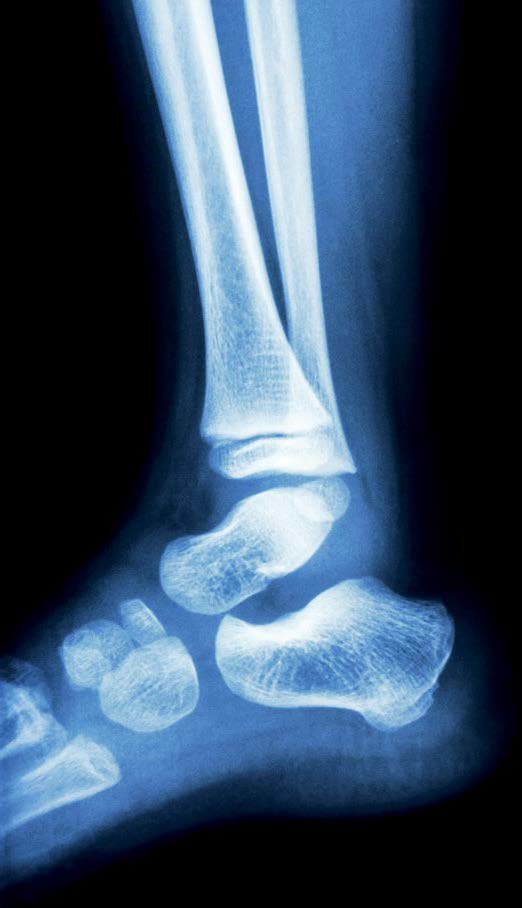
THE first part of this story in our previous issue (December) ended by saying that the very first task of active suspension is to maintain the car’s level and ride height. This is quite easily achieved and does not demand a high degree of sophistication. The vehicle’s level and ride height are sensed by straightforward mechanisms that measure vertical distance. The information is sent to the controller, which will activate either an air or a hydraulic pump to pressurise a height compensator (in the case where the car’s body level drops due to passenger load), which is usually a rubber bladder located between the body and suspension strut. Since the level-changes continuously occur on the move due to the changing road surface or (when cornering) body roll, the level compensation doesn’t have to be a high-speed function.However, with precision sensors and high-pressure pumps, the level control can be adapted to work as an anti-roll device, which is what it does in a fully active suspension.
The other major contributor to an active suspension system is the variable-rate damper. Many car manufacturers refer to the active ride and handling control system as “adaptive suspension” because, in reality, the suspension continually “adapts” to driving conditions. The mass inertia caused by the movements of the car body contributes to instability. Damping these movements in a controlled manner is therefore a critical factor in handling. At present, the finest means of damping is performed by oil-flow resistance inside a telescopic piston-in-tube assembly. The inherent characteristic of this device is to react not in proportion to the force applied, but rather to the speed at which the force acts. Resistance to the piston movement is either by varying the orifice (oil flow passage) or the oil’s viscosity (fluidity). But how can either of these be achieved on the go?
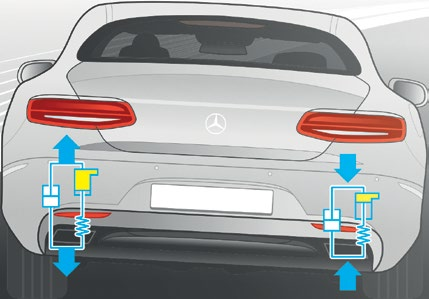
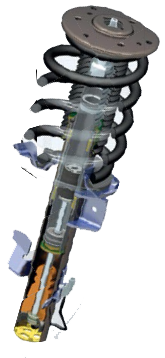
The first method is easier to understand, but not necessarily simple to implement. Electrically variable valves incorporated inside the telescopic damper with ECU-controlled current are able to finely vary the oil-flow orifices to produce diff erent damping rates. It calls for some miniature valves that react to electromagnetic pulses fed through the core of the damper. The second method of controlling the damper oil’s viscosity uses the concept of electro-rheology, which is the manipulation of a specially formulated fluid’s flow characteristics by electromagnetism. The damper fluid consists of oil with microscopic magnetic particles.
When subject to a magnetic field, the fluid’s viscosity changes to directly alter the damping eff ect – softer with the particles dispersed and the viscosity “up”; stiff er with the particles attracted to one another and the viscosity “down”. Magneto-rheological dampers, as they are better known, are pretty much the current state-ofthe- art in suspension damping. Either way, the system relies on a network of sensors that informs the controller about the vehicle’s speed, steering angle, roll, lateral and longitudinal acceleration, and road surface roughness. The software is complex, as it evaluates multiple inputs to produce the precisely right output, which is sent to the actuators for the right damping stiff ness at the right moment. And it all responds in a matter of milliseconds. The active suspension may seem like a lot of complicated high-tech wizardry, but it’s the way to go where suspension design is concerned. Electronic spring-and-damper control is a necessity to achieve the best ride and handling compromise, beyond what basic hardware can do.