Chief technical officer Jon Gunner fills us in and introduces the 21C – the first hypercar from his company Czinger Vehicles.
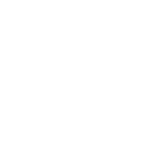
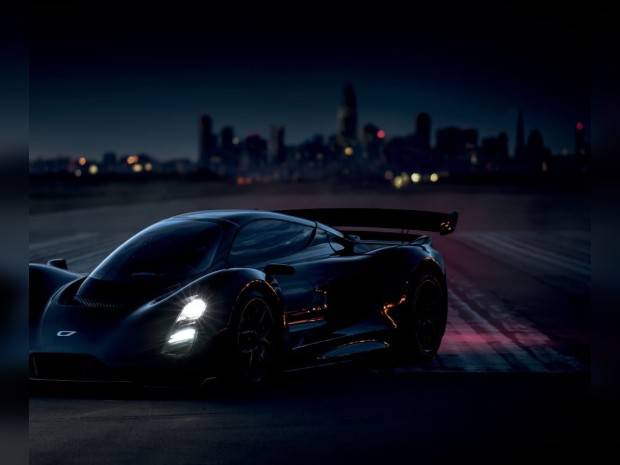
Just over a century ago, on Dec 1, 1913, Henry Ford installed the first-ever moving assembly line for the mass production of cars. The American business mogul was constantly looking for ways to improve the efficiency of the Ford factory, believing that the more cars he could produce, the more he could sell.
While the concept of an assembly line had already been around during Ford’s time, his creation of the moving chassis assembly line significantly ramped up productivity to the point that he could build a car from scratch in 2.5 hours. Previously, it took 12 hours.
Other manufacturers began copying Ford’s production techniques. Since then – and while robots have replaced team assemblers and companies have improved engines, materials and other components – the moving automotive assembly line is a constant even to this day.
Kevin Czinger wants to change all of that.
A former federal prosecutor and Goldman Sachs executive, Czinger is the founder and CEO of Divergent 3D, a Los Angeles-based start-up specialising in the volume manufacturing of advanced, lightweight structures without the use of expensive tools.
In March this year, the entrepreneur and automotive enthusiast burst onto the scene with a bang when he unveiled the Czinger 21C hypercar at a private event in London. The 21C also marked the public unveiling of Czinger Vehicles, a new American car manufacturer named after its founder.
On the surface, the 21C looks like any other souped-up supercar with the only significant difference being the tandem seating arrangement. But a closer look reveals that the 21C is indeed a hypercar, capable of completing the century sprint in 1.9 seconds. More significantly, it didn’t roll off an assembly line. It is printed.
The Peak chats with Jon Gunner, Czinger Vehicles’ chief technical officer, on the world’s first 3D-printed hybrid hypercar.
In layman’s terms, could you tell us more about 21C’s manufacturing process?
This is a completely new process when it comes to creating a hypercar or any vehicle for that matter. Czinger Vehicles has achieved a few world firsts with the 21C.
In 2014, our founder Kevin saw that the availability of supercomputers, object-oriented programming and additive manufacturing could enable
Computational Manufacturing, which became the foundation of the DAPS (divergent adaptive production system). It had evolved by the time I adapted it to engineer the 21C with Kevin and the team. Computational Manufacturing is the basis of our proprietary system. It allows our engineers to introduce a set of requirements for any vehicle’s components and provides them with a geometrical and material solution that has been optimised for its functional requirements as well as those of our manufacturing and assembly processes.
Czinger has developed 3D printer specifications that enable additive manufacturing in larger quantities, so we can create lighter and stronger parts from materials optimised for that specific use.
For example, the engineering team has created a titanium exhaust muffler system that is not only optimised for thermal and noise management but also acts as a key load path for the rear crash requirements. It’s also lighter than a traditional fabricated element.
How is it different from the typical construction of a hypercar?
A typical hypercar uses a spaceframe or composite tub architecture, which requires you to manufacture complex, expensive and inflexible tools as well as assembly fixtures to produce them.
We don’t use tools or traditional assembly fixtures to construct the 21C’s chassis, so there are no traditional constraints. And, as we rely on Computational Manufacturing to create our unique parts and DAPS to assemble the 21C, we don’t even have to design or manufacture tools and fixtures. This gives us flexibility.
In my experience, when you’re locked into using tools, there is little room for adapting parts and fixing issues that crop up.
With additive manufacturing, we benefit from the opportunities that continuous improvement offers.
What are some of the manufacturing challenges of building the 21C?
Strange as it may sound, there are not many challenges. Our manufacturing system, while technologically complex, is highly optimised. However, while it’s not a challenge per se, achieving the highest quality hand-crafted interiors, bodywork and componentry take our artisanal team thousands of hours.
On the flip side, what were the advantages of Computational Manufacturing and DAPS when building the 21C?
Having worked in the aerospace and automotive industries for all of my professional life, tooling is a constant battle. You are essentially firefighting specific issues because of tooling constraints. With our technology and know-how, the team and I can adapt continuous improvements with optimised solutions instead of just workarounds.
While on the topic of manufacturing, how long does it take to build one hypercar?
We have a team of highly skilled artisans, scientists, engineers, software developers and technicians at our headquarters in Los Angeles, California. After years of development and the investment in prototyping, we expect that it will take between 3,000 and 4,000 man-hours – depending on the specifications and individual customisation – to create each 21C. And we’ll only create 80.
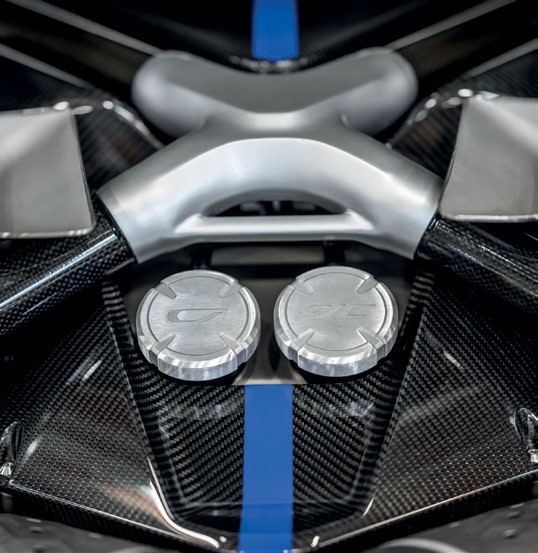
A closer look at the hybrid engine of the 21C.
The battery packs use two lightweight 120kW motors at each front wheel paired to two 2kW/h battery packs. The energy-dense pack is designed to charge and discharge faster than the current production of EV technology.
The batteries are integrated into the chassis to contribute to the overall torsional stiffness, making this a small and efficient way of generating an extra 300 hp to create 1,250 hp overall power (950 hp from the internal combustion engine).
The ICE mounted motor-generator constantly charges the batteries. It can also drive the front motors in serial mode when the batteries are fully charged.
The company-developed 2.88-litre flat crank V8 with twin turbos is the world’s most powerdense production engine. The entire powertrain weighs only 460kg.
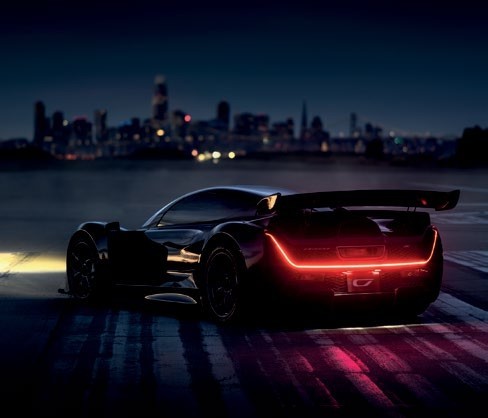
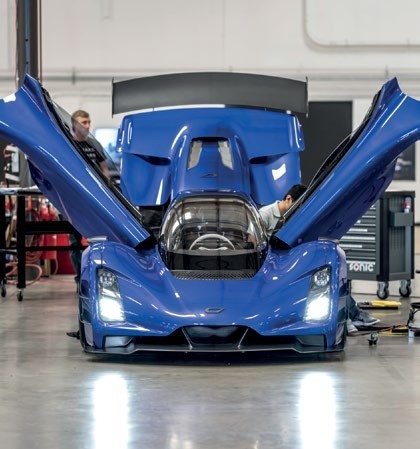
TEXT FARHAN SHAH PHOTOS CZINGER VEHICLES