This technical expert greets every workday with the same mindset: to achieve high standards in Continental’s products.
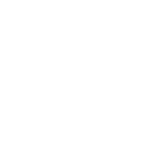
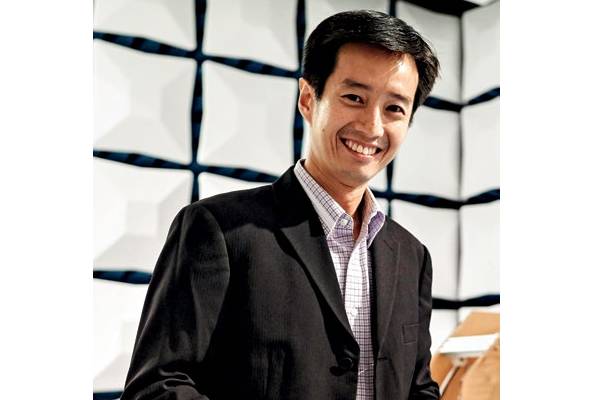
This technical expert greets every workday with the same mindset: to achieve high standards in Continental’s products.

SZE Chen Tat, 40 years old and married with two kids, started his career as an engineer in Continental 15 years ago, when he joined the research and development department of Philips Car Systems (the precursor to Siemens VDO, which was bought over by Continental in 2007).
He is now the Head of Quality for Continental Automotive Singapore, with about 30 colleagues reporting directly to him.
Sze is also the point man for several regional activities across 14 Asia Pacific locations, including business improvement initiatives and the rollout of corporate quality programmes at the various Continental plants.
Sze’s team is also responsible for assessing the consistency of software development on different projects worldwide.
Describe a typical working day.
There isn’t a daily work routine for me in Continental! Every day brings a new set of challenges that make my work interesting.
Being the Head of Quality means I have to be involved in all quality escalations and these can come anytime. Occasionally, this means late-night meetings and teleconferences to resolve customer issues.
What is quality in the context of Continental?
Quality is a vital and fundamental part of Continental’s business.
Our OEM [original equipment manufacturer] customers expect flawless product development all the way to the end of production ramp-up.
Our end customers, the drivers, expect products that function well and have lasting reliability.
Any quality defects will cause our customers to lose their trust in us, meaning we could lose future business.
In Singapore, our focus on quality has always been critical, given our core business is with the European and Japanese automakers.
They have very stringent requirements on quality, their main selling point. Hence, they in turn expect the same unyielding standards from their suppliers, such as Continental.

How do you ensure high quality standards in the workflow?
We developed a holistic approach to ensure quality across the value chain, constantly and consistently involving all our employees.
We organise extensive quality training relevant to both hard skills and soft skills.
In fact, more than 100 training sessions were conducted this year alone!
Company-wide events, such as Quality Week roadshows, are also held to bring about better awareness of new quality concepts or expectations.
Every management team member, including the CEO, takes the chance at every town hall meeting to stress the importance of quality.
Every manager also needs to conduct a workshop with his or her team to brainstorm on their contributions to quality within the company and towards the customer. Regular quality audits are also performed on project teams, and we do not shy from a red status whenever a quality criterion isn’t met.
A robust product testing regime has also been put in place as a final gate.
Which aspects of your work are you most proud of?
Firstly, it will have to be my wonderful team that I work with daily. I built up this team from scratch over the years and we have achieved a lot together.
Secondly, it is an achievement whenever the customer comes back to us with new orders and not defective products. That is the surest proof of excellent quality!
Looking ahead, I still look forward to continuing my career in Continental, as it is a big multinational corporation with many possible opportunities, both locally and abroad.
Having a strong background in quality also helps in my career development, as the work I do cuts across many different functional domains and exposes me to the work in other areas.