Our mechanical engineer gives a refresher on the technology of KERS – Kinetic Energy Recovery System.
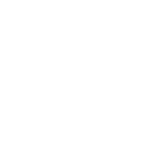
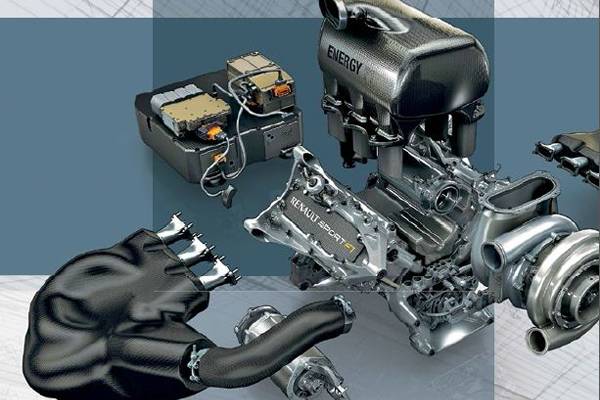
Our mechanical engineer gives a refresher on the technology of KERS – Kinetic Energy Recovery System.
DESPITE initial resistance from the Formula One teams against adopting some form of hybridisation, KERS has since become a standard feature in state-of-the-art F1 racecars.
The concept of kinetic energy recovery is often misunderstood, because brake energy recuperation suggests that the brakes somehow convert mechanical force to electrical power.
Perhaps in a convoluted sense, but the actual process doesn’t work that way.
Think about braking and deceleration as negative energy relative to acceleration.
At the instant the accelerator pedal is released or the brake pedal is depressed, the KERS instantaneously couples the powertrain to an electricity generator or, in some setups, a mechanical flywheel.
This creates a load on the motor and supplements engine braking while the generator output is used to harness another source of energy (such as the battery) for later use. It’s all electronically controlled and it performs with millisecond precision.
The KERS in F1 cars up to 2013 gave the 2.4-litre V8s an extra 80bhp for a maximum of 6.67 seconds, which was useful for overtaking power or slingshot acceleration while exiting a corner.
The latest F1 cars are powered by 1600cc V6 engines with a single turbo.
In addition, there are two electrical Motor Generator Units (MGUs) – one connected to the turbocharger’s shaft and called MGU-Heat (MGU-H), and the other to the 6-cylinder engine’s crankshaft and called MGU-Kinetic (MGU-K).
A hybrid F1 car has a combined power output of about 760bhp, of which 160bhp is provided by the electrical motors.
Compared with the average roadgoing hybrid car, the F1- spec hybrid powerplant is a lot more sophisticated.
Directly coupled to the crankshaft and, ultimately, powering the driven wheels, the MGU-K provides 160bhp of additional horsepower to the crankshaft.
This power boost is a 100 percent increase from what the pre-2014 KERS added to the naturally aspirated V8 F1 engines.
The MGU-K gets its energy from the on-board lithium-ion battery pack situated just behind the driver.
During deceleration, the MGU-K reverses its role and runs off the crank, so as to function as a generator producing electricity. This is how the batteries are recharged.
In essence, the MGU-K functions in exactly the same way as the electric motor in a hybrid passenger car such as the Toyota Prius.
In the meantime, the MGU-H, which is being driven by the turbocharger shaft, also assists in supplying electricity to the MGU-K or recharging the batteries’ energy. But the MGU-H has another little trick.
Since it is coupled to the turbocharger shaft, it can moderate turbine speed in order to prevent overboost.
Even more interesting is the MGU-H’s ability to drive the turbine shaft when it operates as a motor. Every time the turbine needs to spool up when acceleration is required, the MGU-H drives the turbo’s shaft, effectively eradicating any turbo lag.
Driving the turbocharger electrically, at least for a few seconds, to overcome inertia hasn’t caught on yet in the automotive industry.
But something quite similar has recently gone into production in the Audi SQ7 – an auxiliary 48-volt compressor that provides initial boost to eliminate turbo lag.
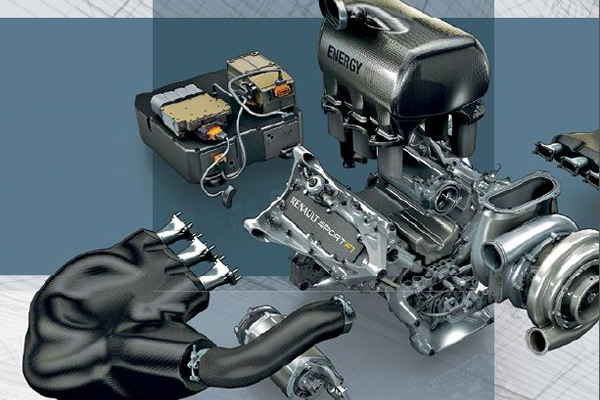
"TODAY’S F1 RACECAR IS POWERED BY A SINGLETURBO 1600CC V6 WITH TWO ELECTRICAL MOTOR GENERATOR UNITS."
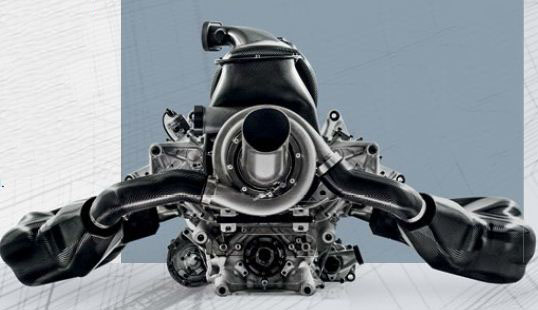