The awardwinning 36-yearold industrial designer bagged the prestigious president’s design award in 2015, for the pour table, which was recently showcased at the alchemists’ exhibition
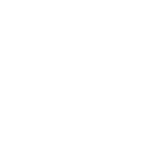
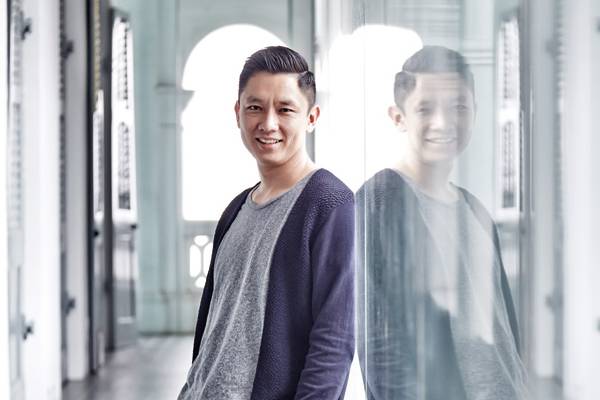
The awardwinning 36-yearold industrial designer bagged the prestigious president’s design award in 2015, for the pour table, which was recently showcased at the alchemists’ exhibition.
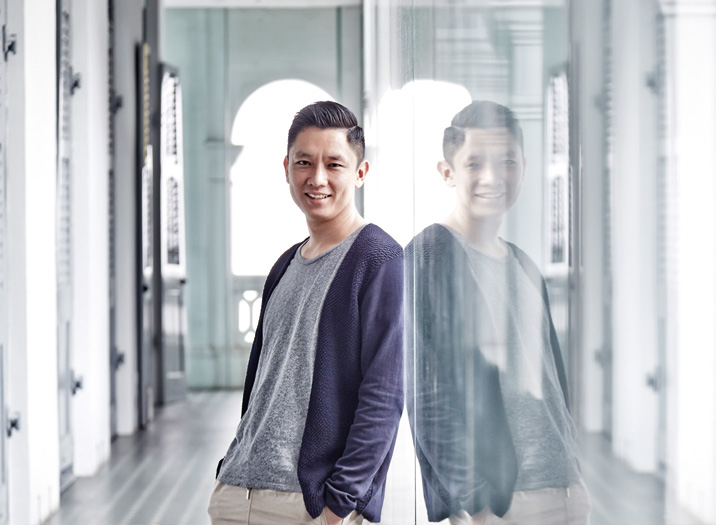
What drew you to the world of design?
I chanced upon a new course at the National University of Singapore – Industrial Design – involving design, marketing and engineering. Thinking it was quite an interesting mix of expertise, I took the plunge after national service. I realised I was good at making things. That was a surprise for me and there’s been no turning back since!
Tell us about the concept behind the Pour table.
What inspired me was the painstaking process of making kueh lapis sagu (a multicoloured layered Nonya cake), which involves steaming each layer before pouring the next one. I experimented with resin and used additives to achieve a viscosity such that it doesn’t run when poured on an open surface. To create the tabletop – without a mould – the resin composite in various colours is poured in succession on a flat surface, layer upon layer, like the kueh!
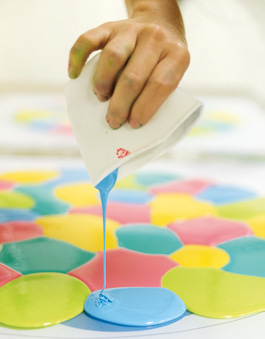
What was the biggest challenge when using this technique?
Timing is critical in the process of working with resin. Between pouring the blobs of coloured resin on top of each other, we had to wait for the material to harden to just the right consistency; a bit like that of a gel. The window period we have is about 20 to 30 seconds. If we are too late, it hardens and will be quite brittle, but if we are too early, the colours will mix. Sometimes, we have to discard a whole piece! So, a lot of calculation, preparation and control are required to make each table. It’s actually a lot like baking!
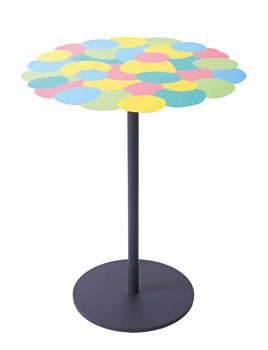
You have quite a diverse portfolio. Do you have a favourite type of project?
I’m more interested in materials and concepts than mediums. My ideas for projects stem from working with materials and understanding them. I like to come up with ideas that subvert how the material normally behaves, by designing a new process to subject the material to.
Any advice for budding designers?
First, learn because you need the knowledge. Then, start bending the rules. If you learn to bend them well, break the rules!