The 27-year-old founder and glass master of Wave Murano Glass shares insights on building a glass empire and why he loves the material.
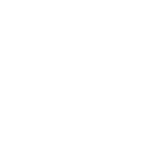
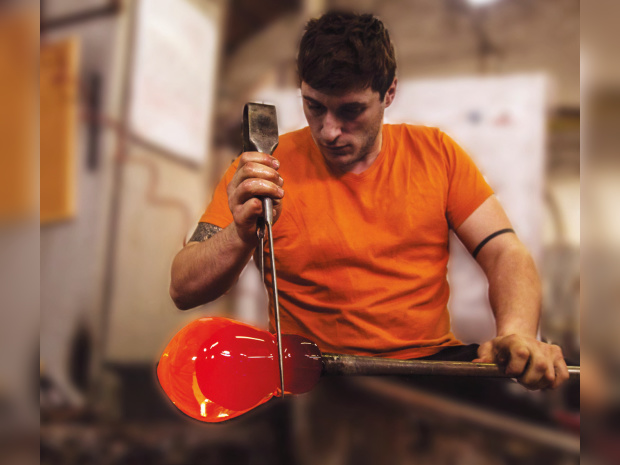
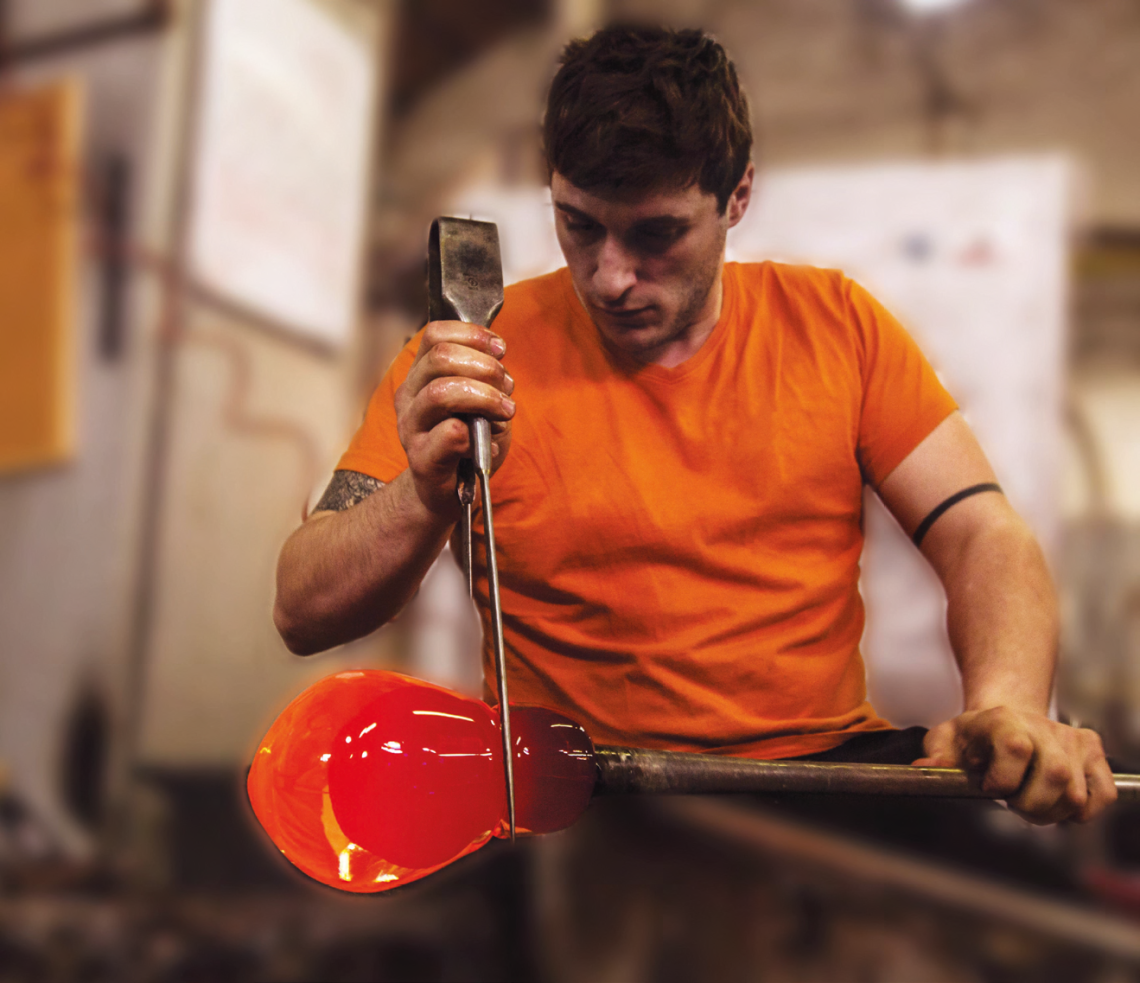
When you’re one brand out of 374 exhibitors at the International Furniture Fair Singapore, not only are your products fair game, but standing out is a tall order. It takes a work of exceptional design, along with visible placement and luck, to get noticed, and these were all in alignment when the glistening sculpted pieces by Wave Murano Glass caught our eye at the Italian Hospitality booth in March.
Compositionally speaking, Murano glass might be a typical soda-limesilica glass, but its working range (the temperatures at which the glass is soft enough to be worked by hand) is wider than that of similar industrial glasses. What makes Murano glass unique is the skill and the know-how required. Muranese craftsmen are some of the world’s most skilled glass handlers, who know how to sculpt, shape and blow the hot, mouldable glass by hand – an artistic technique that was developed and has been passed down over hundreds of years of practice on the Italian island of Murano.
I saw an exhibition by Dale Chihuly at the Museum of Fine Arts in Boston and it truly touched me. I couldn’t understand how anyone could craft such colourful, luscious and transparent visions. My subsequent research after the exhibition led me to read about glassblowing and glass sculpting. I inevitably chose to start my career in Murano because its millenary heritage of artisanal glass won me over.
Sculpting Murano glass in the traditional method is incredibly physically demanding. We are working with heavy incandescent glass masses that take shape as they are moved one wrong turn of the blowpipe could ruin hours of work. The arduous experience encouraged me to better understand the laws of nature behind the material, in order to work it more efficiently, with more artistry. Physics allows me to find new solutions to problems that glass blowers have always dealt with. Even after seven years of working in Murano’s finest workshops, I feel I am still being tutored by my inner physicist to learn, create and innovate in this ancient trade.
I really enjoy the Rostrato technique involved in the making of the Spike vase series. A mass of near-liquid glass is melted as a giant “string” around the body of a vase . The ring of scorching glass is quickly creased many times with a tool called tagliol (sculpting knife), to form a series of square bumps around the vase. A tool called pinzette (a type of large tweezers) is then used to pull the tip of each individual “spike”. All this has to be done rapidly because I’m pulling glass that is almost 1,000 deg C hot. The brutal technique is a game of Russian roulette – the slightest mistake or loss of time means I’ll burn my fingers. It’s a wonderful mental exercise that forces me to focus and be precise.
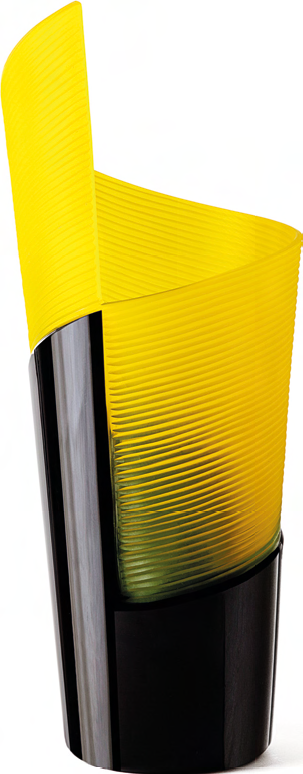
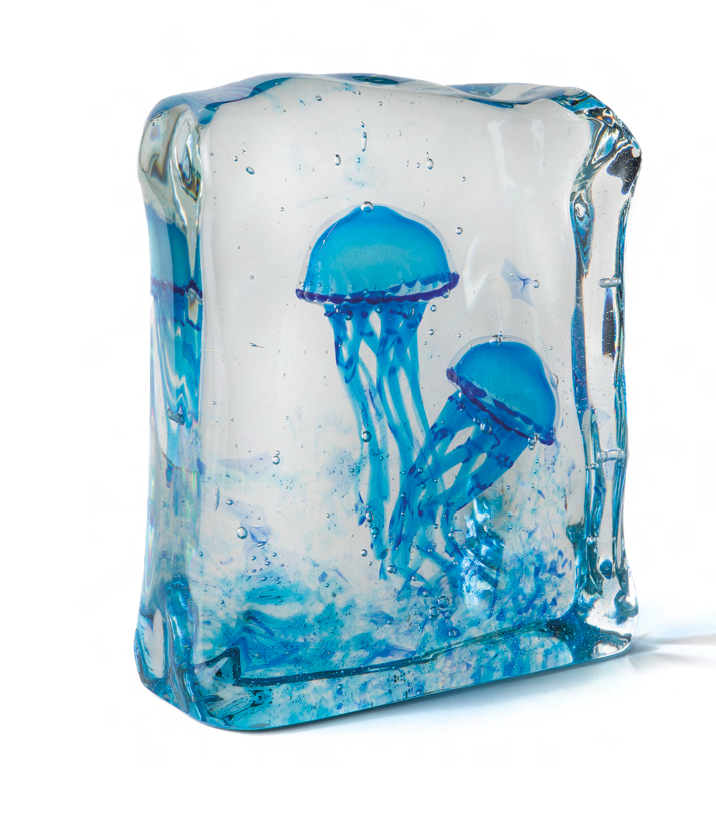
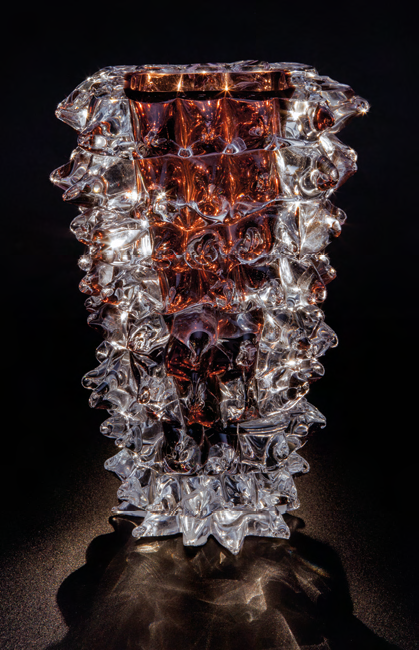
Aquarium is solid Murano glass made using the Sommerso technique, in which a coloured glass is dipped into another molten glass to create a layered effect.
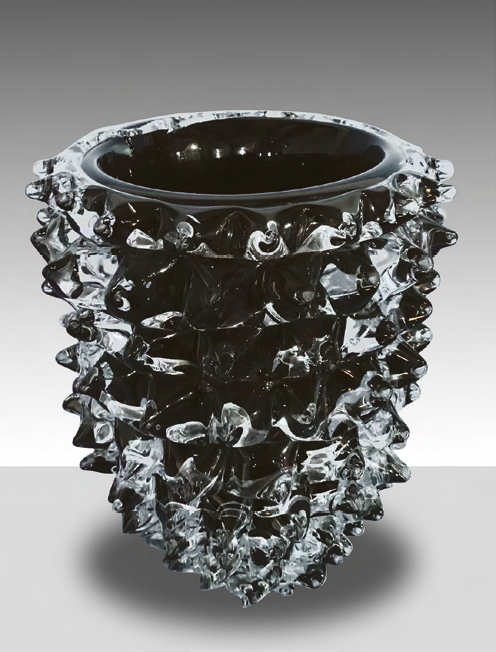
text ISABELLE TOW photos LEONARD FERRI