Handcrafted woodwork is a dying trade in Singapore, but there is hope yet! Young, talented individuals are embracing working with their hands, and creating with wood, turning their passion into bespoke objects. We profile them here.
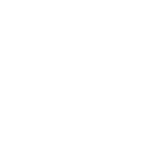
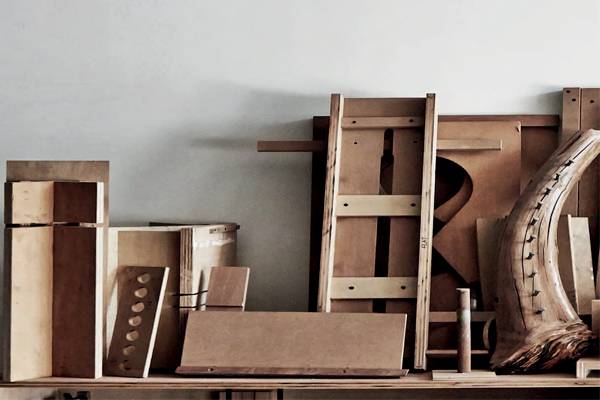
Handcrafted woodwork is a dying trade in Singapore, but there is hope yet! Young, talented individuals are embracing working with their hands, and creating with wood, turning their passion into bespoke objects. We profile them here.
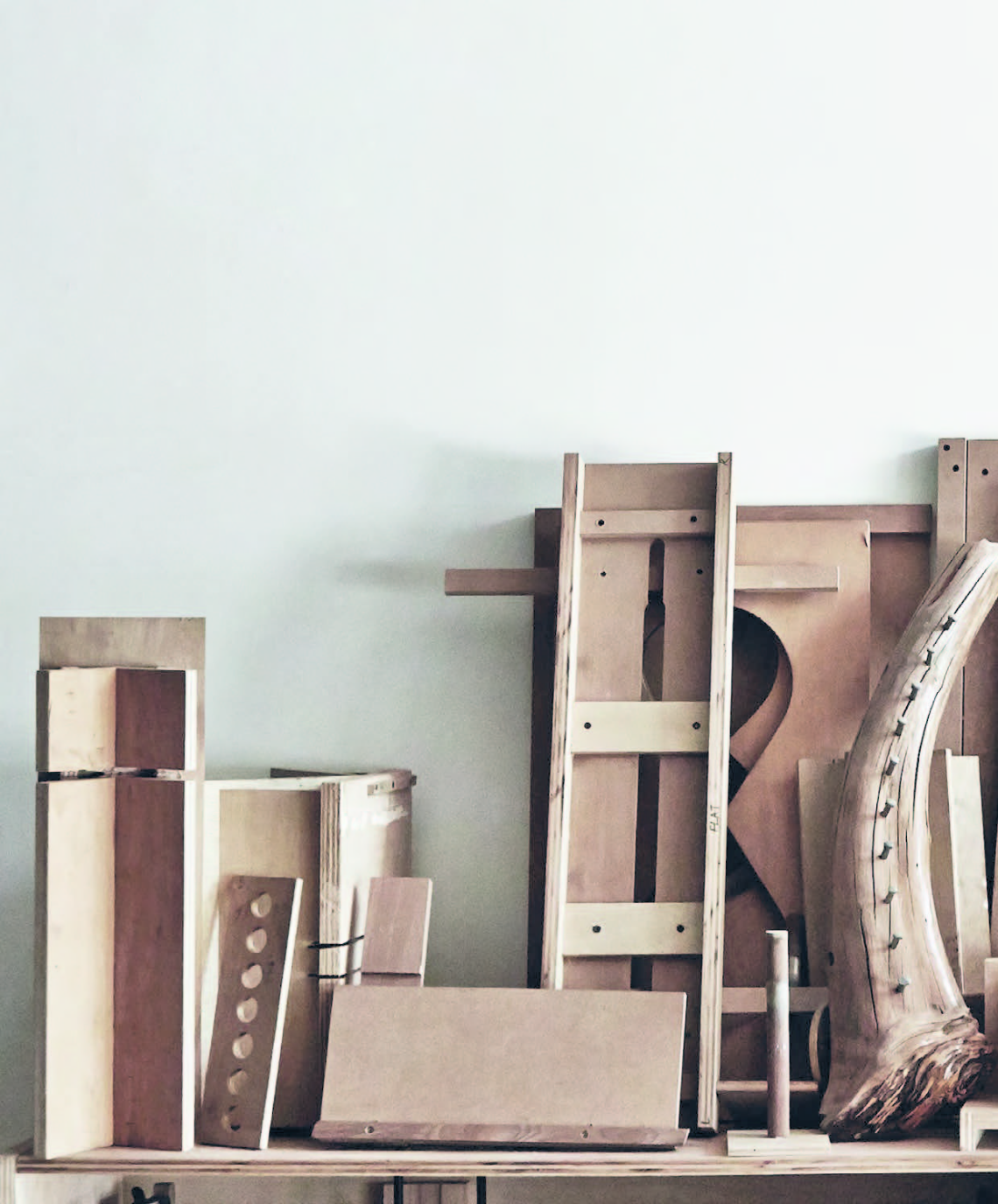
The custom furniture-making studio was set up around 2½ years ago by Rafie Chua, when he decided to leave the corporate world to focus on woodworking and “making stuff”. “During my university days, I made my own furniture,” he says. He attributes his love of making things with wood to the fact that his grandfather and father used to make boats along the Kallang River, and that there were always basic hand tools at home he could play around with. His counterpart, Jonathan Tan, was a chef before working with Rafie seven months ago. He picked up woodworking on his own, watching videos online and tinkering with works. “A lot of it is common sense,” he laughs. But he is good with his hands, too — he had renovated his own home. “I do things myself, rather than have someone else do the job. This way, you build muscle memory, learning how to handle tools and improving,” he says. This applies to his previous job in the culinary arts but, for now, he has chosen wood over food. “I can always cook, but this is something you have to really focus on, and it is very satisfying!”
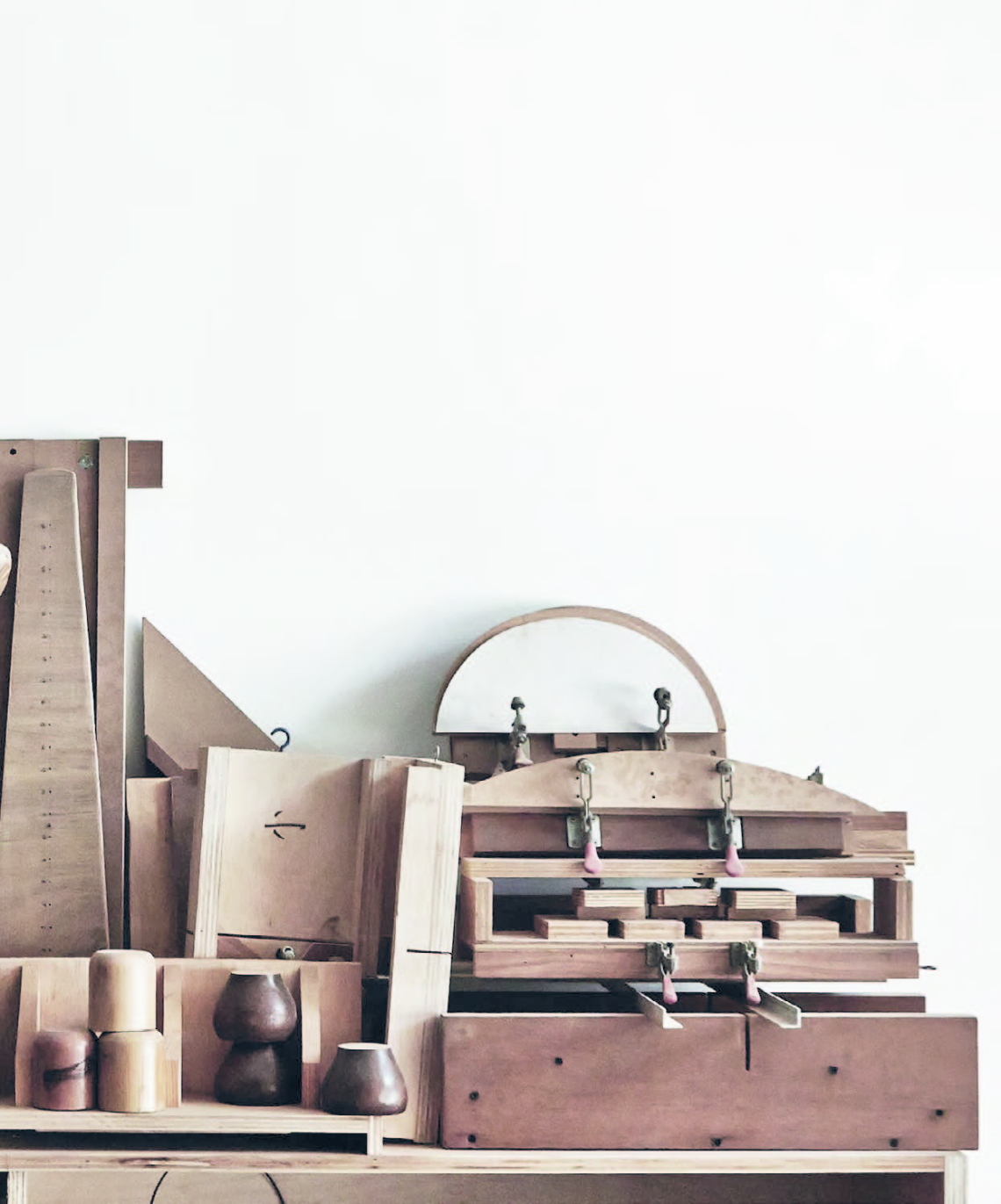
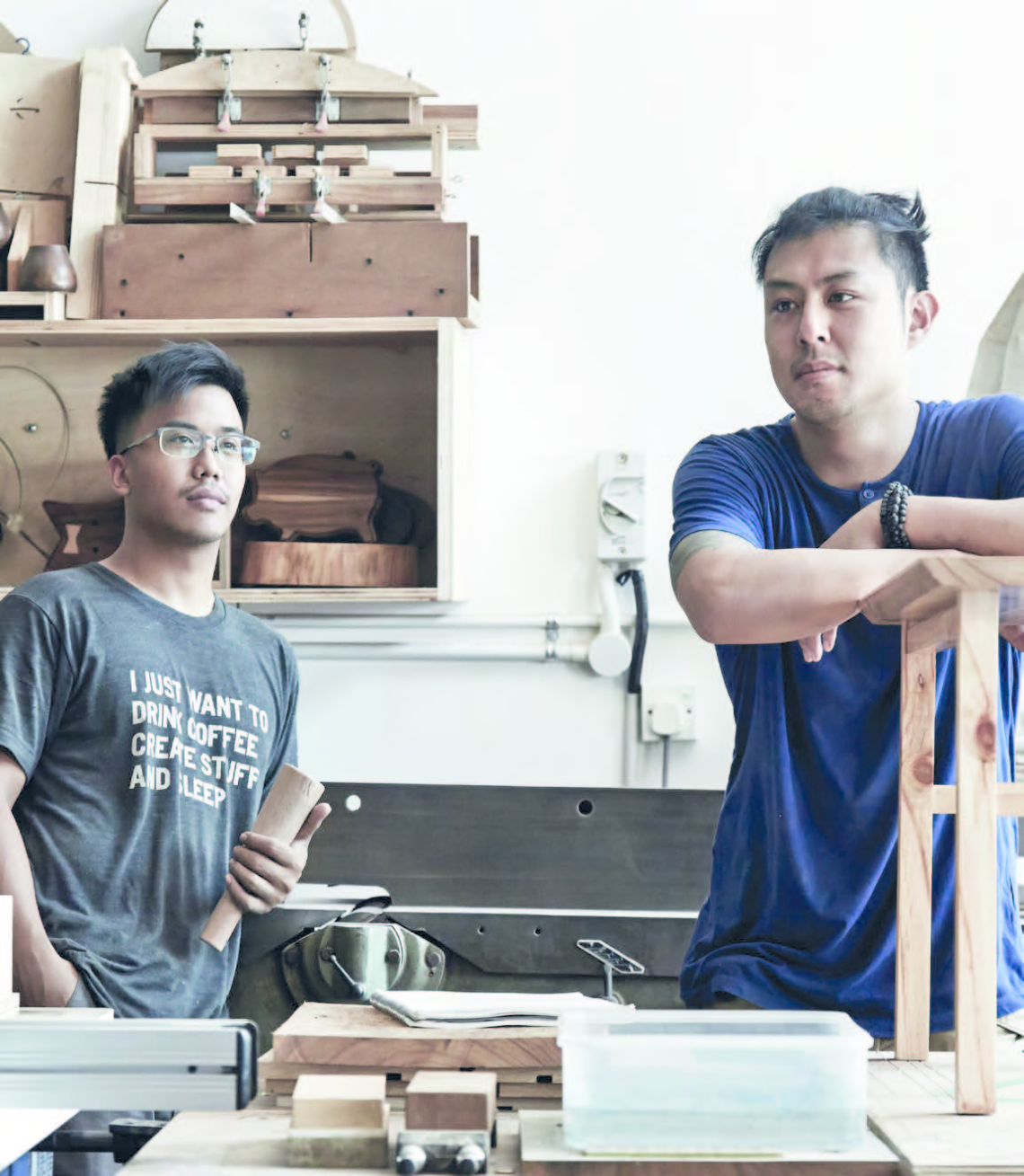
To create solid hardwood furniture and decorative objects, the process begins with milling in the lumberyard where logs get cut into planks. The duo then use hand tools or machinery to clean the wood surface so they can make markings for joinery details. “With joinery, the wood fits together like a puzzle — this was how furniture was made in the past, without nails or hardware,” explains Rafie. Using only compression and at most glue to keep the joints together means that there is no hardware that can degrade; most pieces these days incorporate nails, which tend to not last as long as the wood.
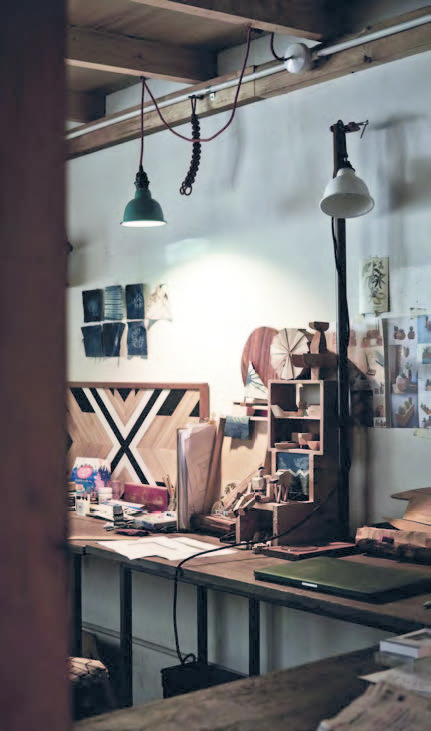
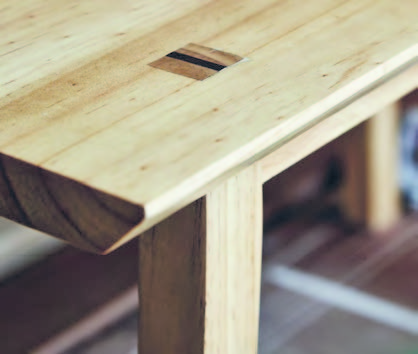
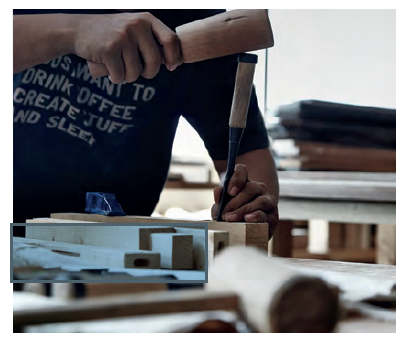
“You can make nice furniture using plywood, but it won’t last and isn’t as valuable, unlike if you use solid wood, and pay a lot of attention to the making process,” says the duo. They are partial to oak, which has a “clean” look suited to most modern homes, is easy to obtain, and is relatively affordable. However, they also work with tropical species, such as nyatoh, teak and khaya. “It’s not so much the type of wood, but the value of the craftsmanship that is important, and good craftsmanship is quite rare in Singapore,” Rafie observes. It is clear that both of them “like the idea of creating with their hands, using the right tools”, but why with wood, in particular? “It has a very long history; humans have always made things using this organic and primary material, and we like its natural and universal beauty,” they explain. Find out more at www.planeandbevel.com
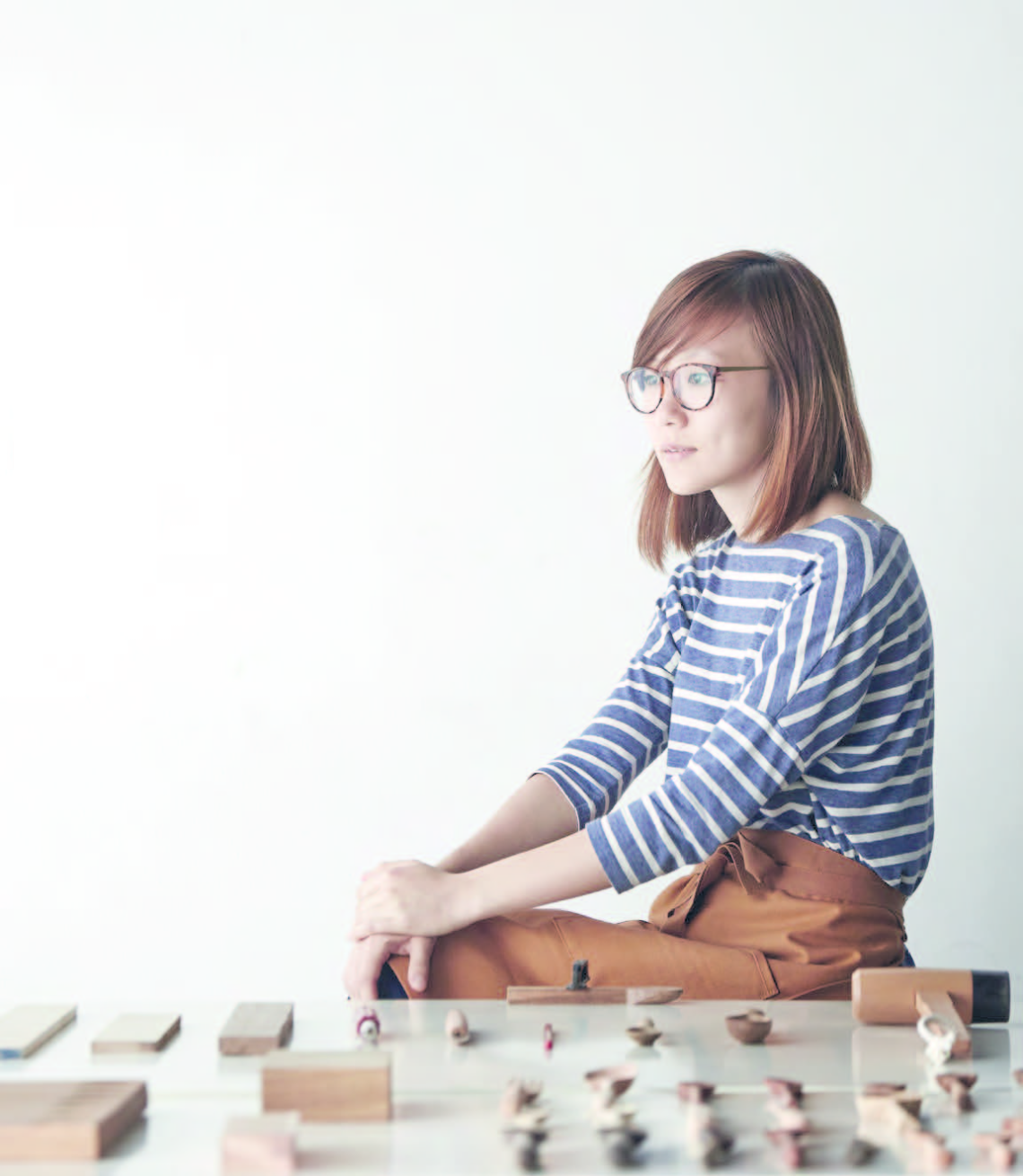
Woodcrafter Ng Xin Nie had her first experience of making things by hand during her university days, when she studied industrial design at the National University of Singapore. But it was only around 2½ years ago that she founded the brand Everyday Canoe, and has since been making homeware, small ornamental pieces and gifts out of solid wood. She started by making spoons, a simple everyday object. “They’re functional and beautiful, and there are a lot of ways to play with its design — I certainly haven’t exhausted them yet!” she says. Now, besides spoons, she makes butter knives, forks, scoops for coffee grounds, brooches, and other small decor objects, as well as custom orders. As her craft revolves around creating smaller objects, she works at home using a few trusty tools: an F-clamp, a gouge — to create depth and curves in the wood, a carving knife with interchangeable blades, a mallet, sandpaper, and food-safe oil — to seal the wood. It takes her around two hours to make a basic spoon, starting from carving it out from a block of wood, to sanding it down, to finishing the piece with oil.
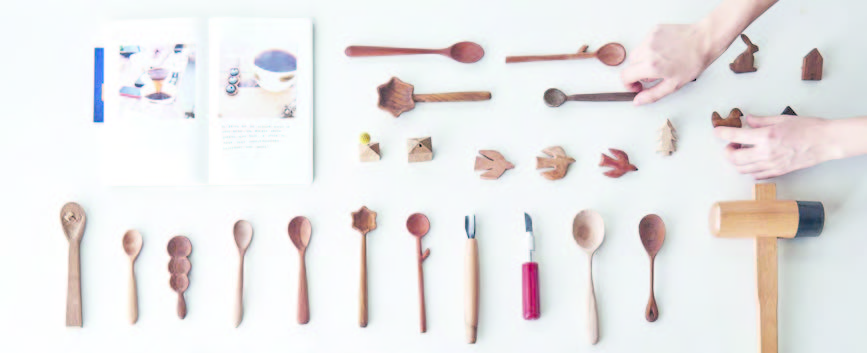
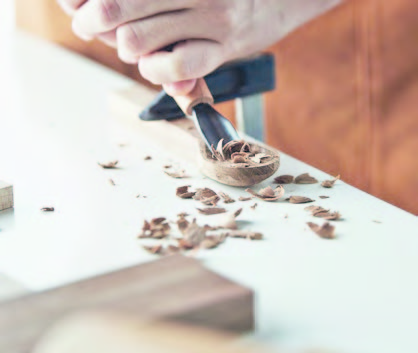
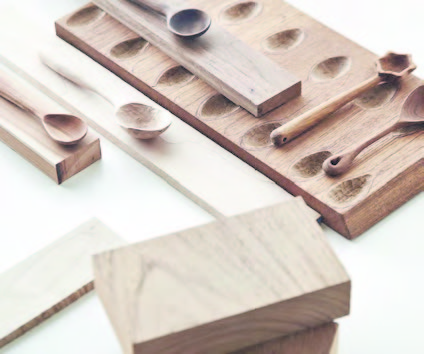
“Wood that is harder to carve produces nicer results — because of the density of the grains, you need more time to coax the wood, but when you finally oil it, the denser grains that show up make it more beautiful!” she enthuses. Besides highlighting the beauty of the material in its design, there are technical considerations, too. The spoons, for example, are shaped according to the direction of the grain of wood for strength. Xin Nie explains that if wood is cut perpendicular to the grain for the narrow areas of a piece, such as the stem or handle, it would be weak. The hardwood that Xin Nie uses are teak, cherry, maple and walnut. She gets offcuts that would otherwise go to waste, from a carpenter friend she got to know through her first job in furniture design. “Although what I use is considered to be ‘reclaimed’ timber, it’s really good hardwood that’s used to make quality furniture,” she says. “I’d love to try other woods, too, and I will keep a look out when I go overseas.” For example, on a recent trip to Japan, she acquired some hinoki (native cypress wood), which she describes as naturally aromatic with a sweet woody smell. While she hasn’t decided what she’ll do with this precious stash yet, her love for wood and creating functional, but meaningful, objects will mean that she will definitely do it justice. Find out more at www.everydaycanoe.com