Making Limoges porcelain is a long process guided by the skilled hands of craftsmen who have mastered rare, centuries-old techniques, and adapted them to the new needs of the industry, ensuring that it is – more than ever – synonymous with prestige and innovation.
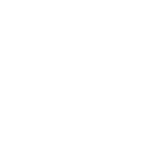
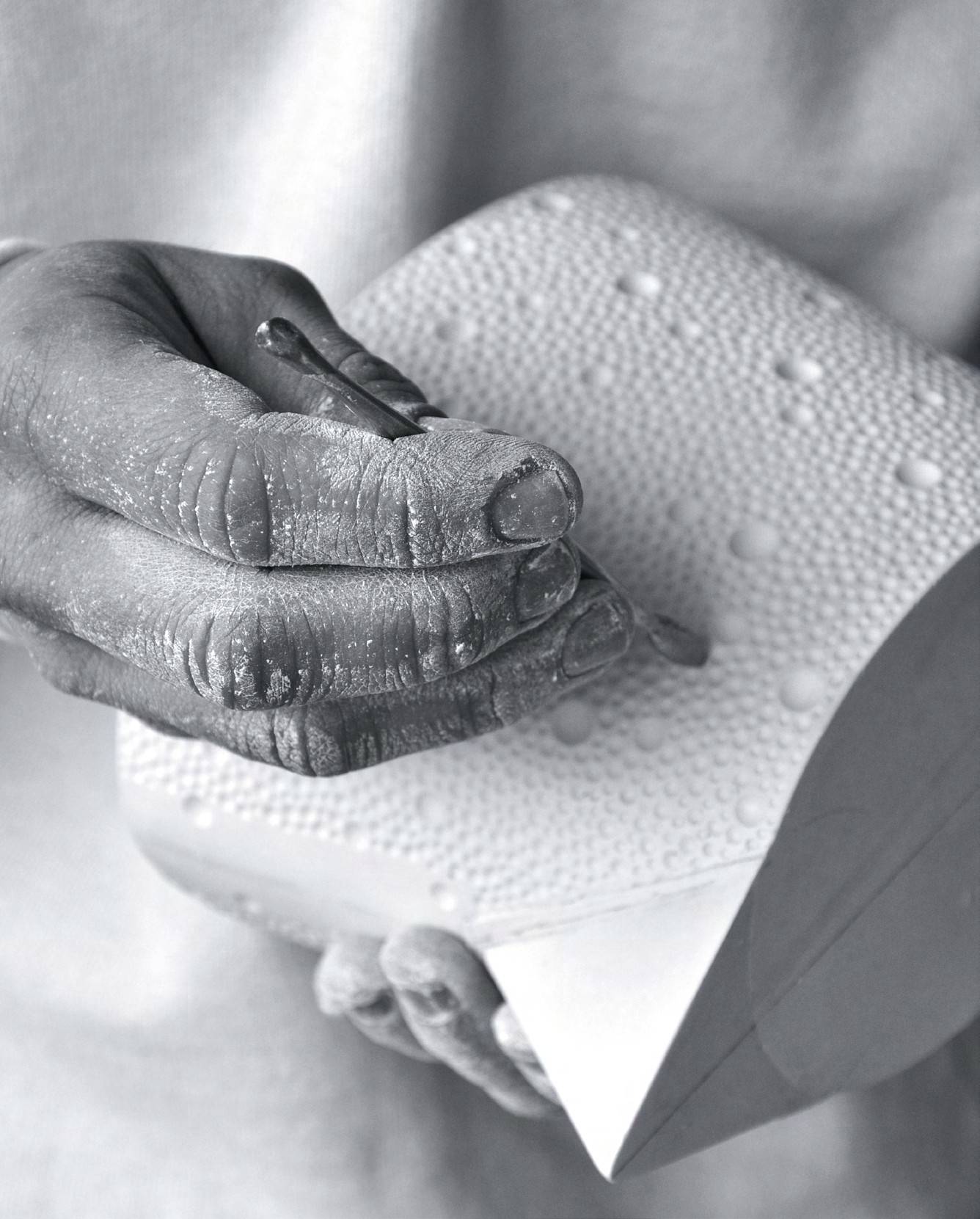
Limoges porcelain is famous the world over. Created 250 years ago, it is unique thanks to its history, quality, creativity and the techniques linked to its production. Located in westcentral France, the city of Limoges itself is at the heart of a land of opulent forests, fresh waters and generous white clay, which are ingredients necessary for making porcelain.
Although porcelain originated in China, its presence in Limoges can be explained by the discovery of a kaolin deposit of stunning purity in 1768. Hundreds of manufactures – such as Bernardaud (today representing 80 per cent of production in Limoges), Haviland and Royal Limoges – were established thereafter, making Limoges a hub of the French porcelain-making industry. It has amassed specific skills and production processes that haven’t stopped evolving, as pastes have become lighter, thinner and stronger.
The singularity of Limoges porcelain lies in the convergence of its unexpected properties, which have traditionally associated it with tableware: pure whiteness, delicacy, hardness, durability, translucency, impermeability, crystalline sonority, ease of cleaning, and the ability to withstand extreme temperatures.
Inalterable oncefred, it is impervious to air, water, humidity and time. Belonging to the ceramics family of earthenware, stoneware, bone china and terracotta, porcelain is also regarded as the most prestigious of its category.
Labour of love
Resulting from the subtle alchemy among various mineral components fired successively at very high temperatures, the realisation of a piece of Limoges porcelain requires nearly 30 steps combining state-of the-art techniques and artisanal virtuosity.
Craftsmen draw, shape, enamel, assemble, decorate or inspect by hand, and rely intensely on their senses: sight, touch and hearing. Following the design, the first step in porcelain-making is to create the object in plaster at a scale 14 per cent larger than the actual size of the finished piece, due to shrinkage during firing. This model serves to make the master mould, which is used to create mass-production moulds in plaster, resin or polyurethane-coated steel.
Sometimes, multiple moulds are needed for one product; the number can go up to more than 50 for the most complex pieces. The basic recipe for porcelain paste is 50 per cent kaolin, 25 per cent quartz and 25 per cent feldspar. This is diluted in water, then ground, mixed, sifted and filtered. Presented in slab form, it is then transformed into liquid, semi-hard or powder pastes, depending on the manufacturing technique required, such as casting for hollow pieces, calibrating for round and raised pieces, and isostatic pressing for flat pieces.
Once removed from the mould, the object dries for between 12 and 24 hours. Spouts or handles are added by hand, and fettling involves removing seams that appear where two or more moulds meet, or eliminating imperfections.
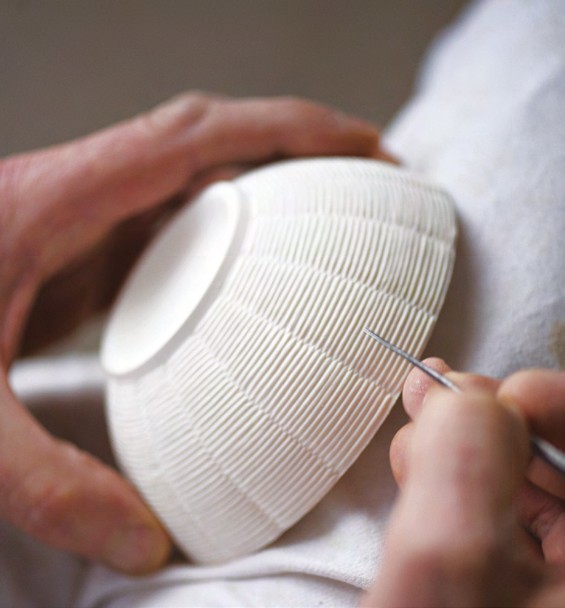
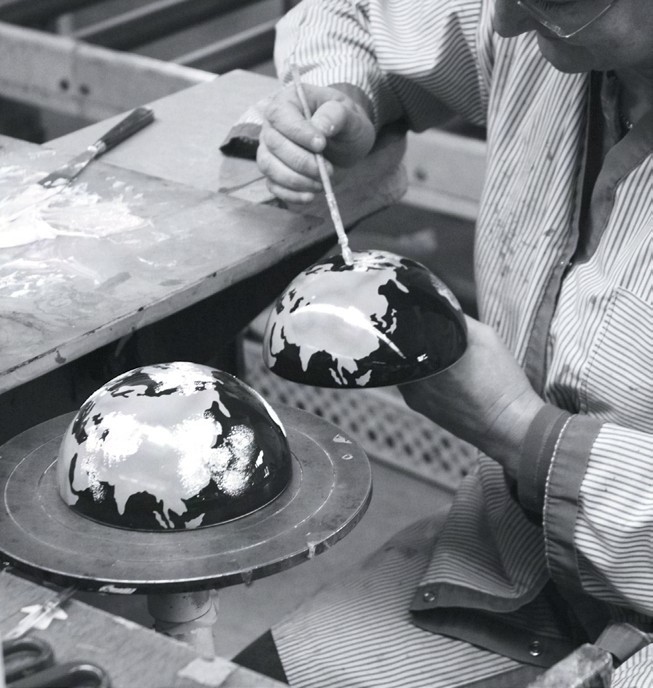
Fire away
The first firing in a gas-fired kiln takes 24 hours at 980 deg C to harden and dehydrate the piece. Then, it is hand-dipped precisely and evenly into a glaze to become smooth and shiny, or left unglazed for a matte look known as “bisque”. The second 24-hour firing at 1,400 deg C vitrifies the paste and glaze.
The challenge is to replicate the original drawing and shades as accurately as possible, as the colours of metallic oxides change during the firing stage, and a deviation of just one degree can mean the difference between success and failure.
Techniques used depend on the type of decoration: lines, fittings and valuable pieces are hand-painted, while silkscreen-printed decals are used for complex motifs, which are transferred manually to white porcelain. Incrustations using acid engraving or gold relief sometimes adorn bespoke work.
Each object is individually checked for quality; over 25 per cent of pieces are rejected due to stains, cracks, spots of missing glaze or deformations, though some defects can be repaired. The artisans spend almost onequarter of their time performing quality-control checks, such as tapping a cup lightly to listen to its resonance, so as to ensure that it meets house standards. It takes one week and over 50 people to complete a teapot, and an additional three to five days for the decoration.
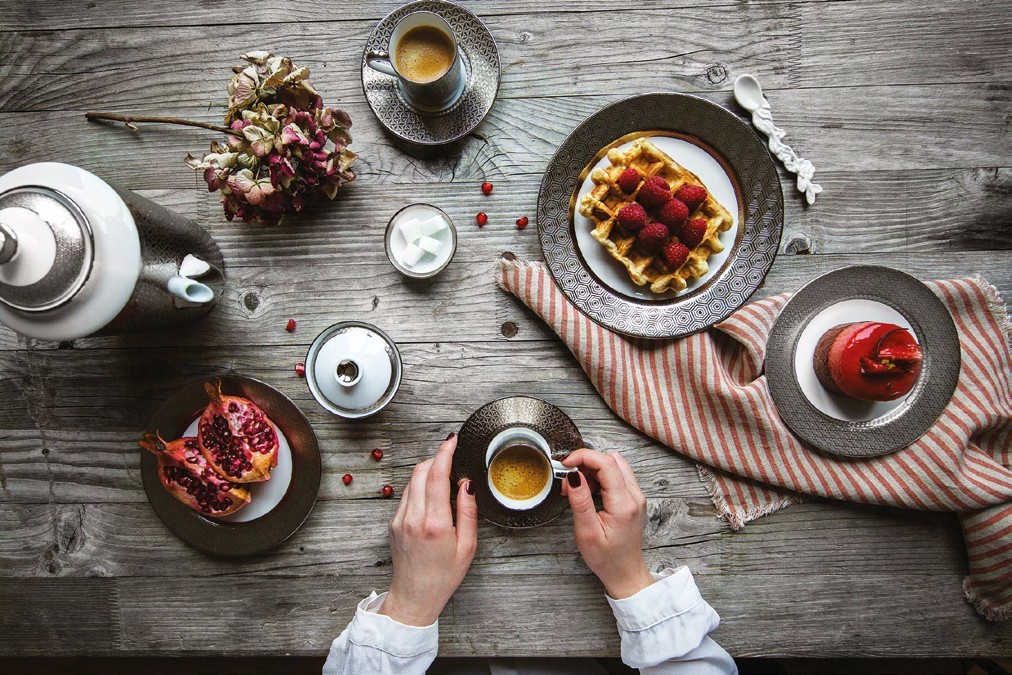
Reign supreme
These days, we find original shapes and decorations, designs that are increasingly geometrical, the use of bright colours, the introduction of a new typology of objects (such as lighting, furniture, trinket bowls, perfume diffusers and jewellery), and complex artworks designed by contemporary artists. All of these are pushing manufacturers to surpass limits of creation, innovation and technical know-how, by questioning a time-honoured material in an original way.
Approximately 1,000 people are employed directly and 1,500 indirectly in the Limoges porcelain industry, a sector in vibrant health that offers jobs in both traditional and hightech domains, with a turnover estimated at more than €80 million (S$127 million). The craft remains attractive to younger generations, as the Limoges area boasts a wide-ranging and complete group of educational institutions – specialised art, design and ceramics schools, research centres such as the AFPI Limousin, ENSA Limoges, CFA Ceramics Limousin, European Ceramics Centre, as well as scientific and technical organisations dedicated to the promotion of ceramics research – granting access to all levels of training and areas of knowledge, from basic trades to experimental research.
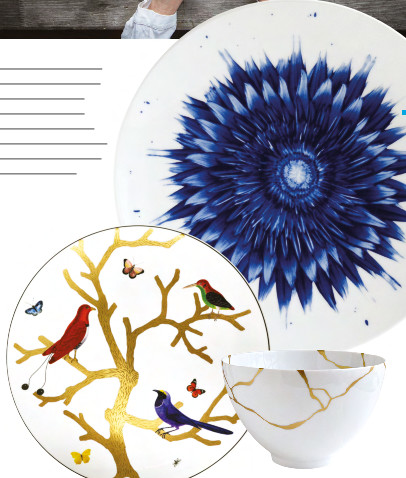
ALTHOUGH PORCELAIN ORIGINATED IN CHINA, ITS PRESENCE IN LIMOGES CAN BE EXPLAINED BY THE DISCOVERY OF A KAOLIN DEPOSIT OF STUNNING PURITY IN 1768.
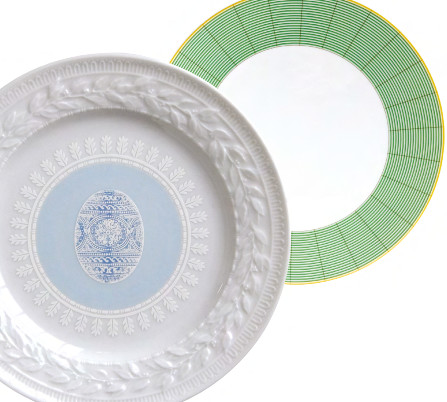
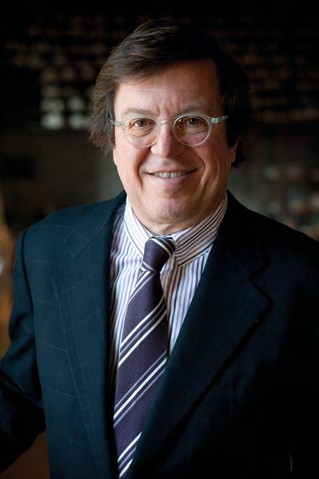
Q&A
WITH MICHEL BERNARDAUD, CHAIRMAN & CEO OF BERNARDAUD
Tell us more about Bernardaud’s legacy in porcelain-making.
Bernardaud was established in 1863 and is still a family business today – I am the fifth generation. I feel very fortunate as I have been able to build on both the legacy of my predecessors and the two-pronged approach that is the company signature: Drawing from the traditions of a heritage craft, we seek to innovate and march to the beat of our own drum. Today, Bernardaud has grown into a major player in the French luxury and international decorative arts scene.
What are the greatest challenges of porcelain-making?
Our greatest challenges are innovation (see the latest Balloon Animals made in collaboration with artist Jeff Koons – we wouldn’t have been able to produce that 10 years ago), and entering new markets (ballistics, cosmetics, architecture). Porcelain, as a material, has so much to offer. It has never been as beautiful and strong as it is today. However, it is quite difficult to produce as it shrinks during firing, and undergoes many deformations we have to master. We spend a lot of time and energy pushing technical boundaries to meet 21st-century challenges. All the ingredients are getting better because all the technologies are also evolving.
Who are the different artists and designers you’ve worked with over the years, and how do they bring a new perspective to porcelain-making?
Bernardaud has always worked with artists and designers. It is completely part of our DNA, and we are very keen on these collaborations because they inspire us to go beyond our comfort zones and bring porcelain to unknown areas. We have collaborated with Jeff Koons, filmmaker David Lynch, performance artist Marina Abramovic, writer Sophie Calle, photographer JR, and so many more.